AHU is a core component in HVAC and ventilation filtration systems, known as air handling units or air conditioning units in some countries or regions. Different industries require AHUs with different configurations.
What is AHU?
The Air Handling Unit (AHU) is a central air management system within centralized equipment arrangements. It functions through ductwork distribution, providing forced air heating and ventilation systems. Generally, it comprises various elements, including fans, heaters, coolers, and filters.

What does An AHU do?
The Air Handling Unit (AHU) primarily operates by rotating a fan, which drives indoor (or outdoor) air to undergo heat exchange with the coils inside the unit. Its primary function is to purify the air by filtering out impurities, thereby regulating both discharge temperature and airflow to uphold indoor conditions such as temperature, humidity, and air quality. AHUs can handle indoor air in recirculation mode and process fresh air introduced from outside.
The main functions of AHU include ventilation and air circulation, temperature and humidity control, filtration and purification, heat recovery, fan and air delivery systems, control systems, noise reduction, and sound insulation.
AHU consists of which parts?
The functional segments of AHU air conditioners generally need to be freely combined according to the user’s specific requirements, and the combinations’ sequence may vary among manufacturers. Usually, AHUs mainly have these parts:
Fresh Air Segment
The fresh air segment primarily receives outdoor fresh air, removing impurities from the fresh air. A fresh air valve is installed with an actuator (on-off type) and interlocked with the fan. Installing a temperature sensor on the shaded side outdoors is recommended for return air temperature compensation.
Filtration Segment
Fresh air filtration typically involves primary (or coarse) filtration, mainly targeting larger impurities. The air filters following the return air segment are generally medium-efficiency filters, which filter smaller impurities. There may also be sub-high-efficiency and HEPA filtration segments for purified air conditioning.
We put pressure switches before and after air filters to check if they’re clean. If the filters are clogged, an alarm will go off.
Return Air Segment
The return air segment is mainly used for mixing fresh Air and Return Air.
The air valve at the return air outlet is equipped with an actuator (analog type) to regulate the return air volume. During seasons with hot or cold outdoor temperatures, while ensuring a certain amount of fresh air, maximizing return air is done to achieve energy savings.
The exhaust air valve at the exhaust air outlet is equipped with an actuator, interlocked with the return air valve actuator, but in the opposite direction.
Temperature and humidity sensors are placed on the return air duct to measure the air’s temperature and humidity. This helps determine the average indoor temperature and humidity, guiding the control of the cold water valve, heating valve, electric heating, and humidification valve.
Chilled Water Coil Segment
The chilled water coil segment is mainly responsible for cooling the air sent to the indoor space, and it can also function as a dehumidifier (optional), with priority given to dehumidification.
A temperature control valve (three-way valve) is installed at the inlet of the chilled water coil. When the temperature and humidity of the returning air reach the desired levels, the temperature control valve is partly closed or shut completely.
Extra chilled water returns through the third path to prevent excessive pressure difference before and after the valve when it’s partly closed or closed. This prevents potential damage to other pipes or pumps and preserves the lifespan of the temperature control valve.
Moreover, a freeze protection switch is placed on the chilled water coil’s surface to safeguard the air conditioning system. It is linked with both the fan and air valve for interlocking operation.
Heating Segment
The heating segment is used during the winter (or for reheating after overcooling during dehumidification). Its operation principle is similar to that of the chilled water coil segment. The two-pipe system shares the same chilled water coil for heating and cooling.
Electric Heating
Electric heating is generally used when the heating segment cannot meet the heat requirements or for reheating after overcooling during dehumidification.
Humidification Segment
The purpose of the humidification segment is to prevent dryness in winter or for special process requirements. The humidification method is usually through wet film humidification or steam humidification.
Supply Air Segment
The supply air segment, also known as the fan segment, delivers air to the indoor space. Actuators (on-off type, optional features) are installed on the air valves at the supply air outlets, interlocked with the fan.
6 tips for choosing AHU
AHU has many functions, but not every usage scenario requires all of these functions. Therefore, you need to choose your AHU according to different usage purposes and environments. For example, in terms of usage, it can be divided into general comfort type and filtration purification type.
Regarding usage scenarios, various applications include comfort environments, industrial purification, biochemical purification, the chemical industry, the tobacco industry, the textile industry, the automotive industry, heat recovery applications, dehumidifier applications, areas with dry weather, etc.
Tip 1 Choose basic type AHU for comfort application
The service object of comfort AHU is people, and its functionality is similar to household air conditioners. The primary function is to regulate the air temperature, providing cooling and heating, simple filtration, and essential humidity control.

This type of AHU does not have strict requirements for airflow; it only needs to remove the cold or heat load from the space.
Common functional segment combinations for comfort AHU:
Filtration segment+coil segment+fan segment.
This configuration is also the most basic.
For the filtration segment, commonly used options include general nylon mesh and low-grade (G3, G4) panel or pocket filters. Filters are typically externally mounted and are often pulled out from the side, although some ceiling-mounted units may pull out air filters from the bottom.
The coil is usually selected based on cooling conditions.
Hybrid segment+filtration segment+coil segment+fan segment
The difference between this configuration and the previous one lies in adding a hybrid segment, which facilitates the connection of outdoor air ducts, allows for easier control of the fresh air return ratio, and simplifies the installation and replacement of air filters.
For applications with higher demands, additional functional segments can be added:
Pocket Filter: Besides low-grade primary filters, higher-grade (F5-F7) pocket filters can be installed. Typically installed downstream of panel filters, they can share the same slide rails for installation.
Activated Carbon Filter: In high-end environments, activated carbon filters can remove odors and smoke from the air.
Humidification Segment: Cost-effective humidifiers such as wet film or high-pressure spray humidifiers are generally used for comfort applications.
Sound Attenuation Segment: In environments where low noise levels are required, such as hospitals, conference rooms, theaters, or broadcasting studios, a sound attenuation segment is usually added. Sound attenuators typically consist of perforated plates and glass wool sound-absorbing panels in comfort applications.
Tip2 Choose AHUs with high air volume, high unit pressure, and high filtration levels for the electronics manufacturing industry
For industries with high requirements for air cleanliness, the primary service object of AHUs is the production process. The electronics manufacturing industry has specific standards and specifications for cleanrooms, with high precision requirements for temperature, humidity, pressure, airflow, and cleanliness. The selection, design, and manufacturing requirements for AHUs are relatively high.
My suggestion is:
Mixed Air Segment + Primary Filtration Segment + Cooling Coil Segment + Heating Coil Segment + Humidification Segment + Fan Segment + Equalizing segment + Intermediate Filtration Segment + Supply Air Segment
This combination is the most common for cleanrooms in the electronics manufacturing industry.
The mixed air segment typically includes air valves to regulate the ratio of fresh air to return air.
The primary filtration segment usually consists of G3 or G4 panel filters. Some customers may request the use of bag filters. The filters for purification AHUs can be configured as shown in the table below:
Cleanliness level | Primary efficiency filter | Medium efficiency filter | Hepa filter |
Class 100 | G4 | F8 | H13 |
Class 1000 | G4 | F8 | H13 |
Class 10000 | G4 | F7 | H11 |
Class 100,000 | G4 | F6 | H10 |
Class 300,000 | G4 | F8 | / |
Class 100,000,0 | G4 | / | / |
Centrifugal fans are commonly used for cleanroom-type AHUs in the electronics manufacturing industry, often of the backward inclined type, with belt drive systems. However, some customers may request direct-drive centrifugal fans to avoid concerns about belt-generated dust. In this setup, the fan motor is connected via a coupling. Fan units without volutes are also widely used in filtration purification AHUs.
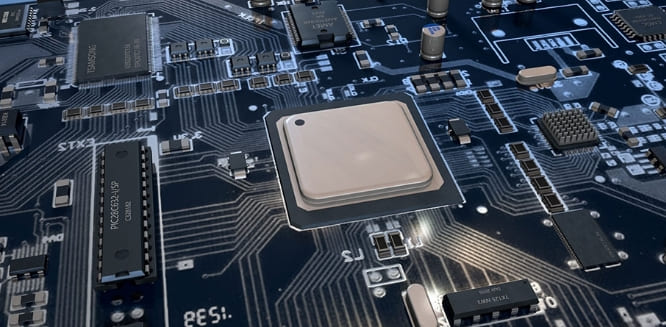
High-grade air filters are typically installed after the fan section, specifically in the positive pressure section, to ensure air cleanliness. Because the unit’s internal pressure after the fan section is higher than atmospheric pressure, there is no need to worry about air contamination due to air leakage from the unit. The equalizing section after the fan distributes airflow evenly and facilitates maintenance.
Customers may choose to increase the level of filtration within the unit based on cleanliness requirements. In high-cleanliness environments, Hepa filters are typically installed at the supply air outlets within the room.
Or we can use an MAU(Makeup Air Handling Unit)
Fresh Air Segment + Primary and Intermediate Filtration Segment + Primary Heating Segment + Primary Cooling Segment + Secondary Cooling Segment + Secondary Heating Segment + Humidification Segment + Fan Segment + Equalizing Segment + High-Efficiency Filtration Segment + Supply Air Segment
As a makeup air unit (MAU) serving cleanrooms, it delivers fresh air directly to the supply air outlet without passing through a return air unit for treatment. Therefore, the enthalpy difference between the incoming and outgoing air of the unit is significant. This requires multiple rows of cooling and heating coils or multi-stage cooling and heating methods.
In the electronics industry cleanroom setting, additional commonly used functional segments for AHUs include:
The spray section: also known as the water washing section or Air Washer, is responsible for humidifying and purifying the air.
Activated carbon filtration section: Used to remove harmful gases from the air.
Tip3 Choose AHUs equipped with dehumidification devices for the pharmaceutical industry
The layout of functional segments in AHUs for the pharmaceutical industry is similar to that in the electronics industry. The difference lies in the specific requirements:
Some rooms require relatively low relative humidity.
Therefore, AHUs are equipped with dehumidification devices. Common dehumidification methods include refrigeration dehumidification and rotary wheel dehumidification.
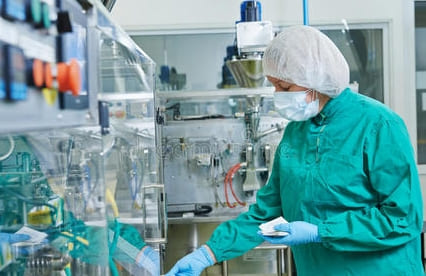
The general layout of functional segments includes Fresh air intake segment + Primary filtration segment + (Pre-) Cooling coil segment + Intermediate segment + Rotary wheel dehumidifier + Return air segment + (Post-) Cooling coil segment + Heating segment + Fan segment + Intermediate filtration segment + Supply air segment.
The (Pre-) Cooling coil treats the fresh air passing through the rotary wheel dehumidifier. After this process, the air temperature rises. The (Post-) Cooling coil is responsible for handling this temperature increase and the load in the room.
Tip4 Choose AHUs equipped with multi-stage filters for hospital cleanrooms
Hospitals have high control requirements for air pollutants, bacteria, and viruses. Therefore, when selecting AHUs, multiple air filters need to be installed.
The layout of functional segments for this type of AHU is as follows:
Fresh air intake segment + Primary filtration segment + Fan segment + Equalizing segment + Cooling coil segment + Heating segment + Humidification segment + Intermediate filtration segment + Supply air segment
Here, I would like to emphasize several points:
The medium-efficiency air filter is positioned in the positive pressure section of the AHU. Due to potential air leakage in the negative pressure section, placing the air filter there may lead to unfiltered air entering the HEPA filter, thus shortening its lifespan.
Considering that some hospital rooms may have bacteria and microorganisms in the exhaust air, it is essential to install primary, medium, and Hepa filters at the exhaust outlets. Additionally, exhaust disinfection devices should be installed to prevent exhaust contamination.
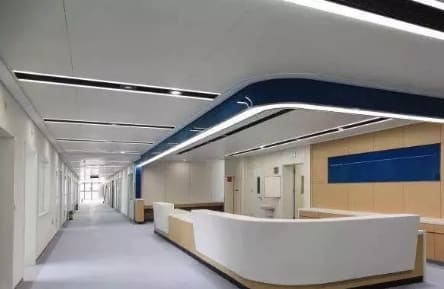
Similarly, to prevent the ingress of unclean outdoor air, it is advisable to install primary, medium, and HEPA air filters at the fresh air intake. As for the return air inlet, it is recommended to install a medium-efficiency air filter to prevent the deposition of hair, textile fibers, and other particles on components such as coils.
Tip5 Choose AHUs equipped with corrosion-resistant and explosion-proof components for the chemical industry
In the chemical industry, where the environment is complex and many harmful gases are released, besides incorporating basic functional segments, AHUs must be selected based on the specific properties of different gases.
When the air contains acidic or alkaline corrosive gases, AHU coils should be constructed with highly corrosion-resistant fins, such as copper foils or stainless steel plates. Alternatively, if the corrosive gas content in the air is low, hydrophilic aluminum foils can be used.

When the air contains flammable or explosive gas components, the AHU’s internal electrical components (such as motors, lights, etc.) and moving parts (such as fans) should be explosion-proof, and the explosion-proof rating should strictly adhere to design requirements.
Chemical or activated carbon filters should be installed in the AHU when the air contains toxic gases. The filling components of chemical filters should be determined based on the specific gases present in the air.
Tip6 Choose AHUs equipped with cartridge filters for the tobacco industry
Characteristics of the tobacco industry include:
- Large air volume requirements for HVAC systems, which operate year-round.
- Some workshops require constant temperature and humidity.
- High dust production during production necessitates high air filtration requirements.
- Tobacco dust tends to be alkaline.
Based on these characteristics, the AHU to be selected should:
AHUs equipped with cartridge filters are characterized by their high-rated airflow, ease of maintenance, and ability to be reused, thus resulting in lower maintenance costs. However, due to cost considerations, some customers use regular bag filters instead.

Due to the large amount of dust production and the susceptibility of coils to blockages, frequent cleaning is required. Therefore, it is recommended to have a larger spacing between coil fins, preferably above 3mm (equivalent to 8 fins per inch).
Tobacco dust tends to be alkaline. Therefore, the AHU’s internal sheet metal components and casing panels are typically stainless steel. The fins are made of copper foil, stainless steel, or hydrophilic aluminum foil.
Last summary
According to various industries’ characteristics and air treatment requirements, the selection of AHUs is highly flexible. Whether it’s in the initial HVAC design phase or later modifications, numerous factors need to be considered for AHU. Whether you’re an engineer, an HVAC designer, or a factory owner, this article can provide insights and assistance.