I have provided HEPA filters, laminar flow hoods, HEPA filter boxes, and other products for many cleanroom projects. Many of these filtration products are used in cleanroom HVAC systems. With years of experience and involvement in cleanroom projects, I deeply understand that the HVAC system is the core component of cleanrooms.
In fact, HVAC is the most complex and critical system in cleanroom facilities. Unlike standard HVAC systems used in building automation, cleanroom projects in biopharmaceuticals, laboratories, semiconductor industries, and purification plants require strict air regulation to better match production needs and ensure quality and progress.
What is HVAC?
HVAC, the abbreviation for “Heating, Ventilation & Air Conditioning,” refers to the discipline of providing heating, ventilation, and air conditioning services. It is an applied science with widespread influence in global architectural design, engineering, and manufacturing industries.

The fundamental theoretical foundations of HVAC lie in heat transfer and fluid mechanics. Its research and development aim to provide more comfortable working and living environments and production environments that meet cleanliness requirements.
What components does the HVAC system have?
The HVAC system includes a temperature, humidity, air cleanliness, and circulation control system. The principles of air conditioning, which supply cold air, warm air, or dehumidification, are similar. They utilize refrigerants that evaporate or condense under the action of a compressor, thereby causing evaporation or condensation of surrounding air to achieve the goal of changing temperature and humidity.
The HVAC system includes:
1. Air conditioning units.
2. Heating, cooling, humidifying, and dehumidifying equipment.
3. Ventilation ductwork (supply, return, exhaust, dust removal).
4. Air purification and filtration systems.
Generally, the HVAC system does not include cleanrooms and indoor facilities.
8 key points about cleanroom HVAC design
After understanding some basic HVAC knowledge, let’s look at the 8 key points about cleanroom HVAC design.
1. Understanding the differences between cleanroom HVAC and standard/traditional HVAC
Unlike standard HVAC systems for office and residential spaces, cleanroom HVAC systems typically have higher air exchange rates. Cleanroom HVAC systems control temperature and humidity to different precision levels to create a comfortable environment.
In addition to comfort, cleanroom HVAC systems differentiate from traditional systems by increasing air supply and airflow patterns, using high-efficiency particulate air (HEPA) filters, and pressurizing rooms.
More air changes
The heightened air supply results in increased air changes per hour, facilitating multiple cycles of HEPA-filtered air circulation within the cleanroom. In contrast, traditional HVAC systems typically provide air changes ranging from 2 to 4 times per hour, while in cleanrooms, it can range from 15 to 250 times or more.
HEPA filters
In the biopharmaceutical industry, microbial contamination is one of the primary control parameters, and HEPA filters can remove ultrafine particles and microorganisms from the air. These filters are crucial for maintaining sterile and controlled environments in critical applications such as research laboratories, medical facilities, and pharmaceutical and testing operations.
The effectiveness and adherence of cleanrooms depend on ventilation. As stated in ISO standard 14644-1, “To minimize the introduction, generation, and retention of particles, cleanrooms must provide a large volume of air filtered through high-efficiency air filters (HEPA or ULPA) to dilute and remove particles, bacteria, and chemicals from the room.” This is the role of cleanroom HVAC.
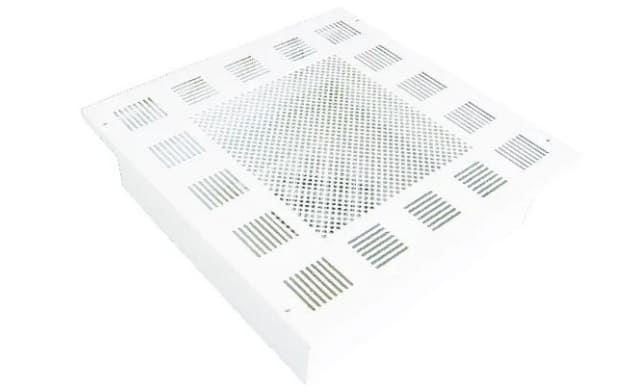
Cleanroom HVAC requires understanding rules, cleanliness levels, airflow, room pressure, temperature, humidity, and analyzing activities. The higher the cleanroom classification within an area and the more precise the temperature and humidity control, the more cooling, heating, dehumidification, and other equipment are required per unit volume.
This results in increased energy consumption due to more air circulation cycles. Therefore, employing HVAC technology in such cases can achieve energy-efficient design.
Cleanroom HVAC must also maintain appropriate pressure differentials to prevent contamination from leaking from lower to higher cleanliness areas.
2. Selecting an HVAC system based on cleanroom design
HVAC design is determined by the required room cleanliness (ISO class), as well as the desired conditions such as temperature, humidity, and pressure differentials, which are dictated by the production processes in the cleanroom and the comfort of working conditions inside the room.
In addition to these factors, project risk assessment, regional characteristics, materials and equipment required for production, a design layout that closely aligns with production requirements to prevent cross-contamination and quality variations, visualization of corridors for inspection, noise control, validation services, prevention of external contamination, requirements for air tightness, requirements for civil engineering and other trades, system durability, and ease of maintenance must also be considered.
3. AHU is not HVAC
People often confuse HVAC systems with HVAC Air Handling Units (AHUs). An air handler is just a single component where the air is heated, filtered, and cooled. It includes cooling, chilled water coils, electric or hot water heating coils, and humidifiers.

As the name suggests, an HVAC system is the entire system, which includes the air handling unit, ductwork, diffusers, HEPA filters, return air, as well as control and monitoring systems.
4. The use of FFU
FFU is an alternative to HVAC systems in cleanrooms with less stringent ISO levels. FFUs are typically used in projects with height constraints, where HVAC systems are impractical due to the space required for installing supply ducts and recirculating air. Suppose you don’t need to cool the room (low heat gain). In that case, FFU configuration is often cost-effective as it directly uses air from the main building, eliminating the need to install a second ceiling above the cleanroom to create a plenum.

Typically, FFUs cannot generate the same level of pressure head as Air Handling Units (AHUs) and cannot establish positive pressure cascades. Another consideration is the noise generated by the fans inside the FFUs, which can be problematic for large cleanrooms with many FFUs.
5. Determining Airflow CFM
Your cleanroom provider will inquire first: How many air changes per hour are needed to calculate the required airflow (CFM: Cubic Feet per Minute)? Answering this question is difficult. While online calculators for cleanroom air changes per hour (ACH) exist, they provide only approximate estimates.
Factors to consider
In fact, cleanroom HVAC engineers must consider more data when calculating to arrive at the appropriate CFM. Determining CFM is challenging because it must account for the following factors:
- Cleanroom cleanliness standards, typically defined by the cleanroom class (such as ISO 5-6-7-8, GMP ABC, etc.), dictate the level of cleanliness that must be maintained, measured by the number of particles per cubic foot of air.
- The number of individuals present in the cleanroom significantly impacts its cleanliness. Cleanroom operators contribute to 70% to 80% of the contamination within the space. As the occupancy increases, so does the level of contamination, necessitating more frequent air changes per hour.
- The size of the cleanroom and the number of internal rooms.
- The machinery, furnishings, and materials within the cleanroom can emit airborne particles and pollutants.
- Heat gain.
- The movement of staff and materials entering and exiting the cleanroom.
6. Temperature and humidity
Accuracy in maintaining temperature and relative humidity (RH) (+/-) is also crucial in HVAC design.
The air conditioning must compensate for the heat generated by occupants and equipment. Therefore, it is essential to know how many people will work in the cleanroom, the installed equipment, and the heat they generate (in watts).
Additionally, depending on the production processes carried out in the cleanroom, temperature and humidity control can be critical at times, requiring precision to ±0.25°C and ±2%.
7. Differential Pressure
The pressure requirements for ordinary indoor spaces are moderate. However, cleanrooms have different pressure requirements for different areas to prevent the infiltration of external contaminants (outflow of internal pollutants) or the mutual influence of different substances in different cleanrooms (zones).

Most cleanrooms are maintained at positive pressure (except when handling hazardous products, where negative pressure is required). This means air flows out of the room rather than into it, preventing unfiltered air or airborne particles from entering the cleanroom. The HVAC system generates the pressure differential to maintain pressure cascades between cleanroom zones and the external environment.
Consider fume hoods and BSCs
In the design of cleanroom HVAC systems, fume hoods or biological safety cabinets (BSCs) must be considered, as some BSCs exhaust air to the outside, resulting in indoor pressure imbalances. To maintain the correct pressure in the cleanroom, fresh air must be supplied to compensate for the air output.
8. Measurement and detection equipment are indispensable
In a controlled environment like a cleanroom, numerous parameters require continuous monitoring to maintain optimal conditions. Various monitoring tools are indispensable to validate the HVAC system’s effectiveness.

Appropriate, precise, and stable instruments are essential components of cleanroom engineering. Among them, differential pressure transmitters, temperature and humidity transmitters, air velocity transmitters, airflow measurement devices, airflow hoods, particle counters, etc., are indispensable products for cleanroom facilities.
Last summary
Cleanrooms may face challenges typical of any experimental or manufacturing environment. Since HVAC plays a central role in cleanroom operations, it’s crucial to plan, select, and manage the installation and commissioning of HVAC units tailored to your specific needs in collaboration with your preferred HVAC contractor/supplier. As an experienced and leading manufacturer of cleanroom components and HVAC filters, you can get a stable, clean, and dust-free environment via our products and services.