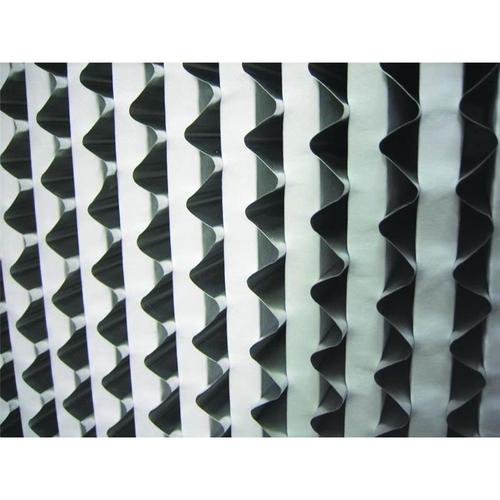
What is a deep pleat HEPA filter?
The deep pleat HEPA filter is a type of HEPA filter usually used to indicate the type of HEPA air filter that uses aluminum foil or cardboard as a separator. And because the pleat is along the depth direction of the filter, it is called a deep pleat.
Why does a deep pleat HEPA filter need a separator for its pleated filter media?
When paper-based filter material is used, the area of the filter paper in the filter has to be tens of times the windward side of the filter to achieve high dust volume capacity(service life) and low resistance, for which the pleated filter paper needs to be separated in layers in some way.
The earliest HEPA air filters used corrugated aluminum foil separators to separate the filter paper, and this structure was used in almost all HEPA filters until the 1970s.
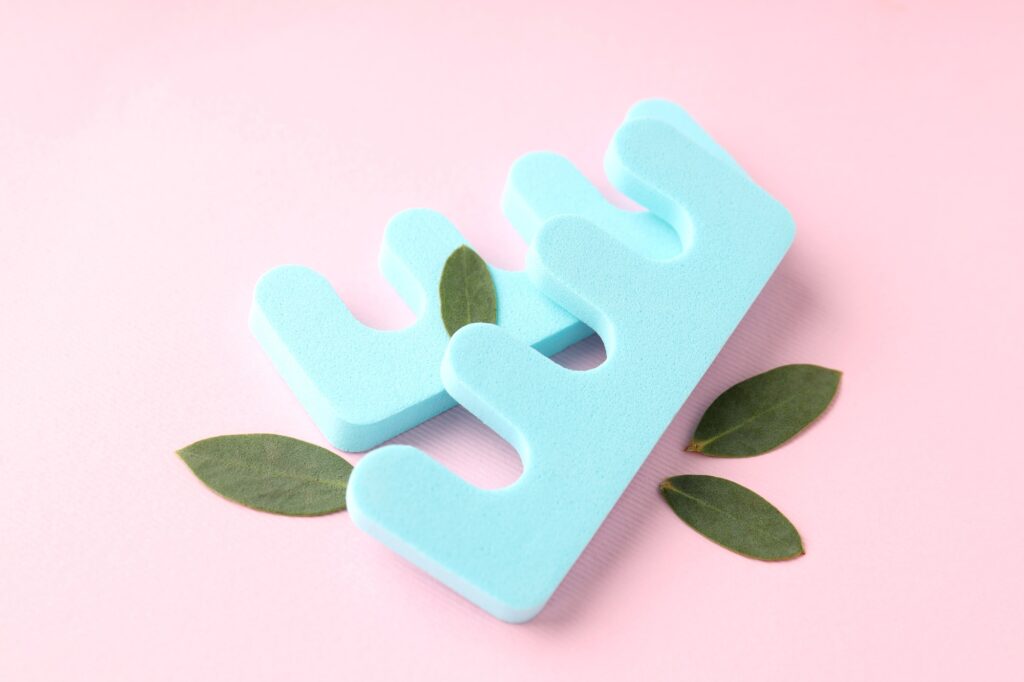
Most HEPA filters are still constructed with separators, and many air filter manufacturers use white cardboard as separators to save money. But, paper separators are a safety hazard because it is combustible.
In Japan, some air conditioner air filters are also separator structures.
In some cases, for safety and temperature resistance requirements, it is still necessary to use the filter with aluminum separators.
It is used as the end filtration equipment of various filtration systems.
Deep pleat HEPA filter media adopts ultra-thin glass fiber filter paper as filter material, folded with glue board paper, aluminum foil, and other materials as separation, sealed with a new type of polyurethane sealant, galvanized plate, stainless steel plate, aluminum as the outer frame, and each unit are strictly tested.
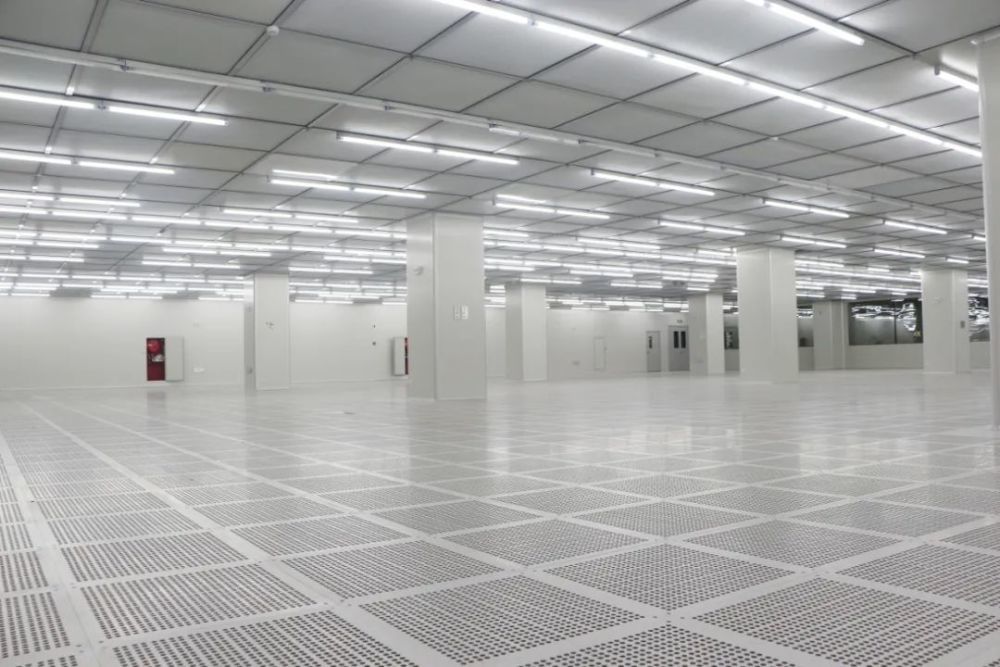
It is suitable for end filtration in clean rooms, commercial and ventilation air conditioning systems, and end filtration in food processing plants, biological containment laboratories, high technology manufacturing, hospital operating theatres, safety cabinets, research laboratories, and other industries.
The role of the separator, sealant, filter media, and other parts of the deep pleat HEPA filter
Separators
The corrugated separator can precisely maintain the distance between pleats to maximize the use of filter media with minimal resistance. In corrosive environments, the aluminum foil separator can be used. The edge of the separator is folded to prevent the filter media from breaking. The thin separator can have more pleated layers, thus expanding the filter media area and increasing the airflow.
Sealant
The seal is completed with sealant inside the frame to prevent side leakage around the perimeter. The sealing layer completely seals the edges of the filter media and the separators, sealing all possible channels for leaks to occur.
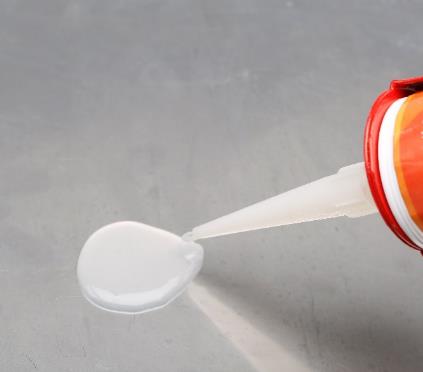
Filter media
Filter media is made of high-density paper with ultra-thin glass fiber or uses high air volume PP filter media (PP material is generally used in the spraying workshop, which needs a lot of air exchange and not high requirements for purification environment, such as 10000 level).
The filter media pleat layer should expand the filter media’s effective area to reduce the filter media’s filtering speed and resistance.
Frame
Frame: wooden frame has been eliminated, and now the use of metal frames, including galvanized sheet, stainless steel, aluminum, and other metal materials.
The main features of deep pleat HEPA filter
1. use of ultra-fine glass fiber filter media.
2. Scanning test unit by unit.
3. High-temperature resistance up to 400 degrees or above.
4. low resistance, high efficiency, and long service life.
5. 180-degree pleats on both sides of the filter material, folded to form a wedge-shaped pleat layer, two indentations when the filter material is bent so that it forms a wedge-shaped box pleat layer at the end of the partition, the wedge-shaped box pleat layer can prevent the filter material from breaking.
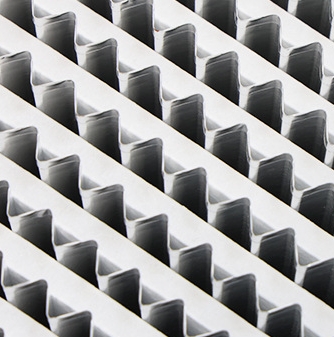
6. All around is sealed by special sealant, which makes the sealing of the deep pleat HEPA filter very good, and there will be no leakage in the working process, which will not affect the everyday filtration work.
7. The corrugated separator of the deep pleat HEPA filter can ensure the distance between the pleated layers and make maximum use of the filter media under slight resistance.
General knowledge about deep pleat HEPA filters and clean room
The deep pleat HEPA filter is for different particle sizes (0.1-0.3um) of fine particles, and the filtration efficiency is up to 99.99999% or more.
Some people always correspond the efficiency level of the filter with the level of the clean room, as if the use of ultra-high efficiency filters can achieve a hundred or even ten levels of cleanliness.
This concept needs to be corrected.
The HEPA filter is the system’s core but is not the only condition to ensure cleanliness.
The efficiency of the HEPA filter is only one of the necessary conditions, and it is also the most accessible condition to achieve.
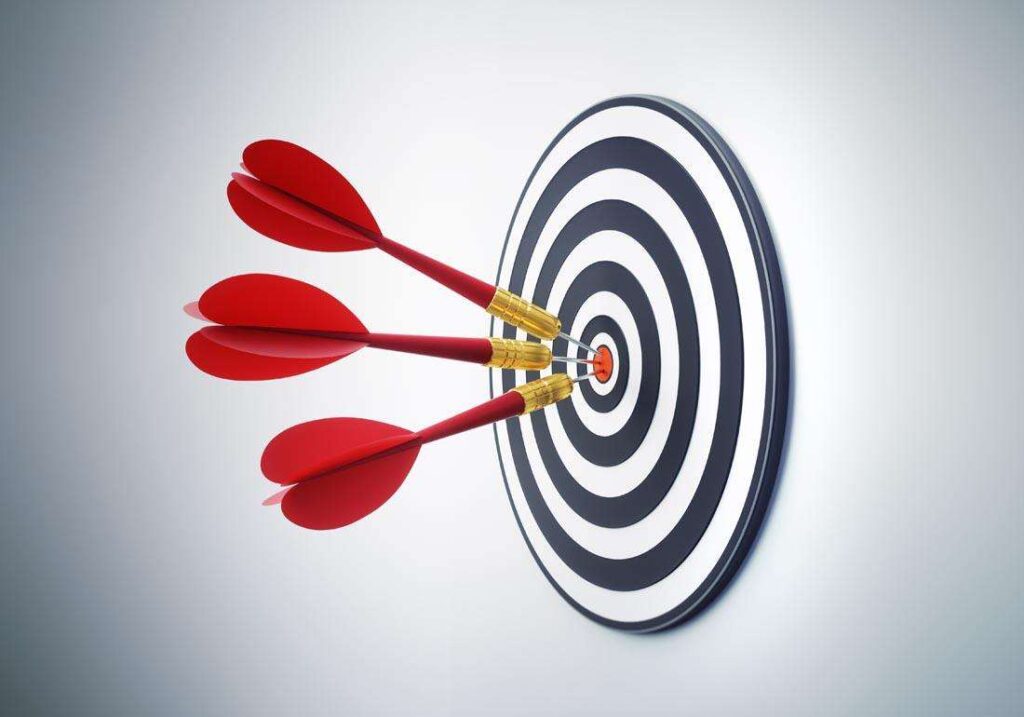
And to achieve the corresponding level of the clean room should also have many necessary conditions, such as airspeed, the number of air changes, doors and windows sealing, personnel access to the clean room control, and many other aspects. Only these aspects are all up to standard to ensure the clean room cleanliness requirements.
Deep pleat HEPA filters replacement interval
The primary filter is generally replaced once every 2-3 months, and the medium-effect filter is replaced once every six months so that the life of the HEPA filters can be more than one year.
But to protect the use of high-efficiency particulate air filters and to protect the safe operation of the clean room, many smart owners of clean rooms every month to replace the primary filter every three months to replace the medium and sub-efficient air filters so can ensure that the high-efficiency particulate air filter life of more than three years (or even five years), and because the replacement of the new filter resistance is small, the air conditioning load is significantly reduced. The filter replacement cost is much smaller than the electricity required to run the air conditioning.
Frequent pre-filter replacement can make the air conditioner run under a low resistance load, saving many electricity costs.
The service life of deep pleat HEPA filters
For a cleanroom in-production operation, the value of the end HEPA filter is not high. It may not add up to the shop’s output for a few hours, but the risk and overhead cost of replacing the end high-efficiency particulate air filter will be high.
When replacing the HEPA filters, production has to be stopped, and the owner of the clean room himself can only calculate the loss of production stoppage, and this loss is higher than the cost of the HEPA filters.
Replacing HEPA filters is a meticulous operation, and anything in the cleanroom can be expensive, and the loss of one part can be higher than the cost of the entire air filter.
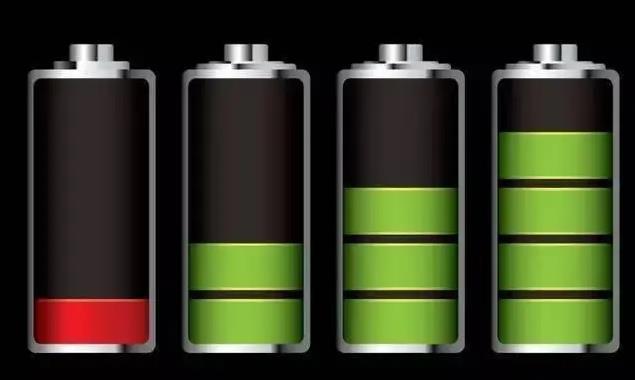
After replacing the HEPA filters to be tested by professionals, the air conditioning system is sometimes commissioned after a trial operation. Testing, commissioning, and trial run, three costs added together, may not be comparable to the price of the air filter.
Intelligent owners of the clean room always want to extend the life of the HEPA filters as long as possible, not to save a few dollars. They want to avoid a bunch of trouble due to replacing the filter.
Extend the life of deep pleat HEPA filters
The most fundamental way to extend the life of a deep pleat HEPA filter is to keep dust out of the pre-filter.
Replace the pre-filter generally without stopping production, without commissioning, so experienced owners will spend their attention and money on pre-filter and protection level intermediate filter.
For class 10K and 100K clean plant, pre-filter selection G4, the intermediate can choose F8 filter (colorimetric method 95%) so that the end of the deep pleat HEPA filter life is generally up to 2 years.
The F8 filter is the most common pre-filter for non-uniform flow clean rooms in foreign and new domestic projects.
The life span of deep pleat HEPA filters in special situations
In some cases, the service life of the deep pleat HEPA filters is not due to the consideration of resistance but other factors.
Suppose there is hydrofluoric acid in the plant, and the workshop air conditioning is not a Ventilation System. In that case, the glass fiber filter paper in the HEPA filter will be corrupted by the return air, and the HEPA filter must be replaced regularly for safety.
Some large pharmaceutical plants, every year after the rainy season, replace the high-efficiency filter to prevent any possible mold contamination on the filter.
Some biological laboratories and laboratories dealing with hazardous materials will require new HEPA filters for reliability before carrying out a unique and vital subject.
Deep pleat HEPA filter VS mini pleat HEPA filter
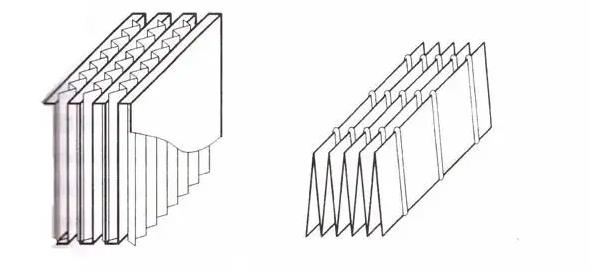
- The material of the filter separator is different: the deep pleat uses aluminum foil or paper separator, and the mini pleat HEPA filter uses hot melt glue as the separator.
- The suitable environment is different: deep pleat HEPA filter is ideal for low-level non-unidirectional flow projects with a variety of purification equipment and clean plant, generally, 10,000 to million-level purification workshop; high requirements for the clean plant will choose a small, lightweight, easy to install mini pleat HEPA filter, commonly used in ten to ten thousand level purification workshop.
- Different temperature and humidity resistance: deep pleat HEPA filter has better resistance to high temperature and humidity than a mini pleat HEPA filter.
Another difference between the two types of filters is their size and shape. Deep pleat filters are typically larger and rectangular, while mini pleat filters are smaller and more compact. This can make mini pleat filters more suitable for applications where the area is limited, such as portable air purifiers or small HVAC systems.
Except for some special occasions with high-temperature resistance and high safety requirements, mini pleat HEPA filters can replace deep pleat HEPA filters.
High temperature resistant deep pleat HEPA filter
Another unique application of deep pleat HEPA filters is high-temperature resistance. After adding high-temperature resistant sealant and using high-temperature resistant gaskets, the high-temperature resistance of the filter can be significantly improved. For example, it can be made to work continuously in an environment of over 400 degrees. And it does not affect its filtration efficiency and performance.
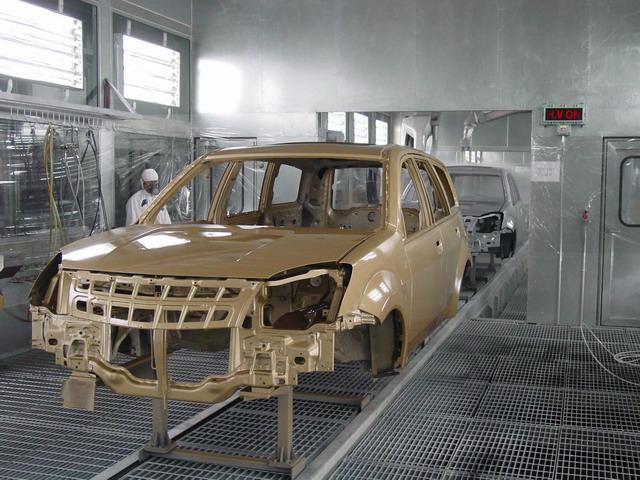
It can be applied in:
- The terminal of the air conditioning and ventilation system (end filtration and hot air type high-temperature oven)
- High-temperature coating line
- Clean baking room
- Purified ovens
- Food baking equipment
- High-temperature sterilization equipment, such as pharmaceutical plant high-temperature sterilization equipment
- Other ventilation and air conditioning systems with high fire protection requirements or high ventilation temperatures
With the advantages of high filtration efficiency, low resistance, high dust volume capacity, and large air volume, deep pleat HEPA filters are commonly used in various purification equipment and clean plants.
The standard number of pleats of deep pleat HEPA filters is determined by two key factors: the separator’s height and the separator’s tightness in filter media assembly.