Air Filter manufacturers specialize in manufacturing air filters of various sizes, specifications, and efficiency for different air filtration systems.
In recent years, air filters have gradually come into the production and life of people.
Finding a professional, experienced air filter manufacturer with a sound management system is significant for buyers.
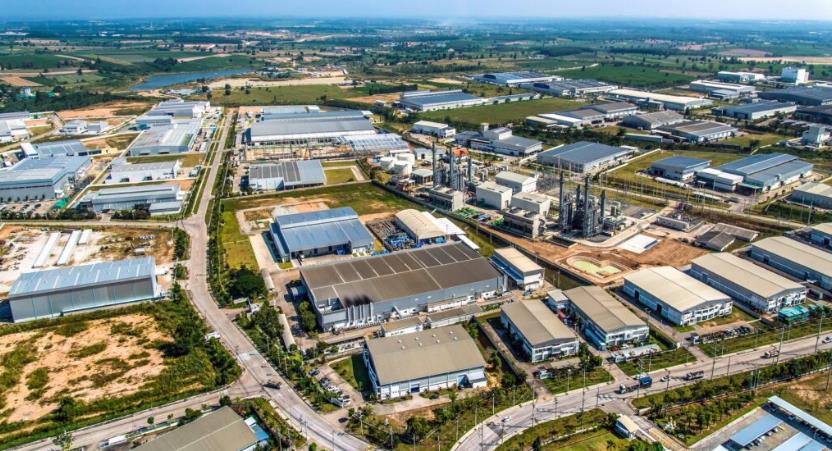
Air filters to remove pollutants
Air filters can adsorb, decompose or transform various pollutants, airborne particles, and harmful particles in the air and effectively improve indoor air quality.
They are used in the home, medical and industrial fields, and some air filtration products like air purifiers, air cleaners, dust collectors, and other filtration systems or filtering systems in different areas with different filtration requirements.
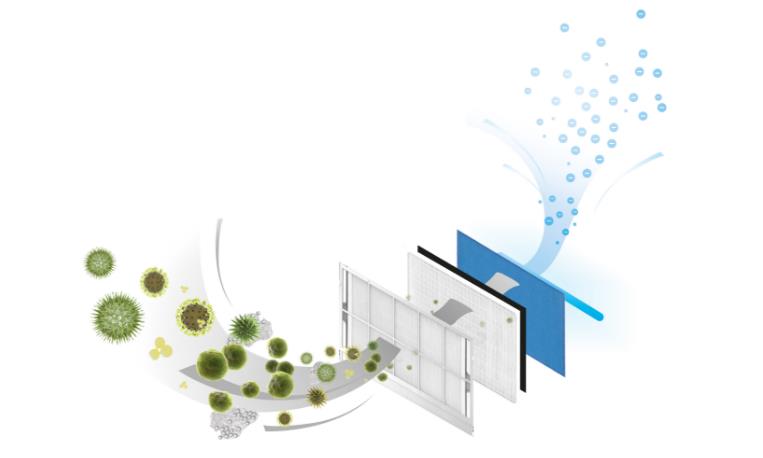
In producing some precision products, many factories usually need to keep the production workshop clean so that the air entering the clean room needs to be filtered, so industrial air filters can strictly control the internal environment of the clean room.
Various air filters for different pollutants
There are two main air pollutant types: solid objects and gaseous chemical pollutants.
Solid objects can contain particles ranging from centimeter-sized to micron-sized particles, such as hair, fibers, dust, airborne particles, pet dander, etc.
Gaseous chemical contaminants also include many different types.
To filter different types of air pollutants, it is common practice to use various filters.
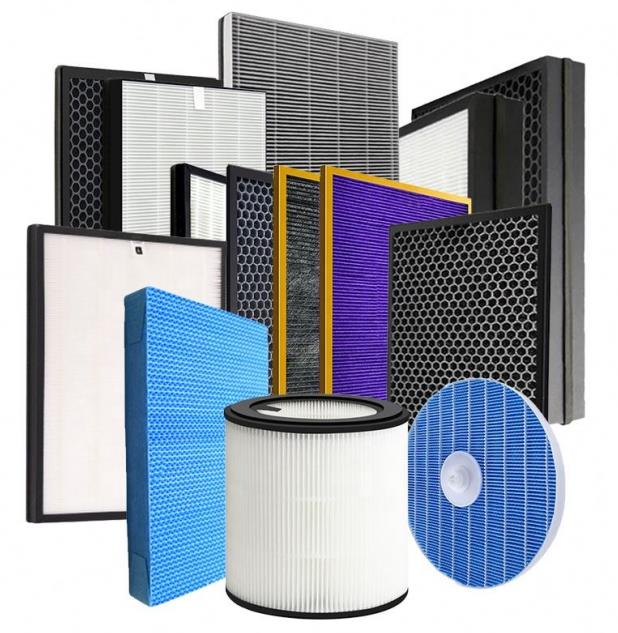
For example, air filters made of non-woven materials are usually used to filter solid objects such as fibers, hair, dust, airborne particles, etc.
Depending on the adsorbent, air filters containing chemical adsorbents filter various gaseous chemical contaminants via some chemical reactions.
The quality of the air filter is directly related to the filtration effect and air quality. And the manufacturing of air filters is a very rigorous and complex process.
Qualified air filter manufacturer
A qualified air filter manufacturer has to meet at least the following criteria:
Manufacturing environment
All medium and HEPA filters are produced in class 100,000 clean rooms to avoid different degrees of contamination from the production environment before the filters are delivered to customers.
Production and process equipment
- The assembly line production method improves production efficiency, and filter quality can be better controlled.
- They are adopting the most advanced international automatic filter media folding production line and glue filling machine for operation, avoiding all kinds of quality problems caused by the equipment during the production of filters and significantly improving the quality rate of products.
- The air filter gasket uses a hand-pasted sealing strip, which eliminates the phenomenon that the filter is not tightly pressed together with the installation site, resulting in leakage around the filter.
Online quality control
In the mass production of each process of the air filter, the first piece should be confirmed and then produced after the quality inspection is confirmed.
The quality engineer must check once when producing 1-3 pieces of products in each process in batch production to avoid rework and scrap in large quantities due to other factors in production.
A quality inspection should be conducted for each of the following processes in time and in sections to stop production if problems are found and re-produce after passing the check.
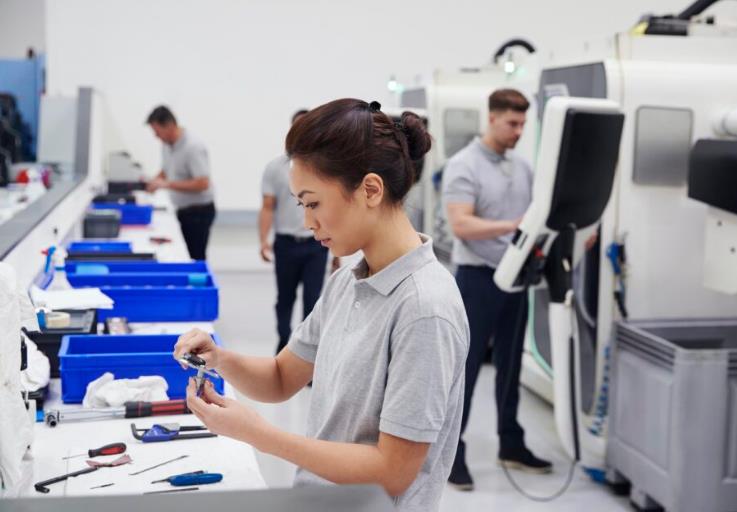
A quality inspection should cover the qualified semi-finished products, unqualified semi-finished products, and qualified finished products of each process with markings to facilitate effective differentiation.
The inspector takes random samples in the workshop and inspects them according to the relevant standards of this product. Make original records and issue inspection reports.
Normal air filter standards
Depth: The deviation of depth dimension is -0.2/-1.2mm.
Diagonal: The diagonal of each end face of the filter is equal.
Perpendicularity: The end face of the frame should be perpendicular to the side, and the deviation should not be greater than 3°.
Appearance:
- No deformation, oil stains, or scratches on the outer frame.
- No gaps at the four corner splices, and the four corners must be polished smoothly without burrs.
- No deviation in the color of the guard mesh and no rust, and the guard mesh must be close to the air inlet surface.
- No damage to the filter material and no linting.
- The surface of the glue is smooth and free of dents and piles.
- The sealing tape is firmly and neatly pasted without distortion.
The outgoing inspector takes samples of the products to be shipped out for inspection on the same day.
Visual inspection of the appearance, measure the size and check the inspection records and update records.
Complete management system
From the production environment, 5S, raw material inspection, production process, personnel training, finished product quality control, customer complaints handling, and other aspects must establish a complete and mature management system.
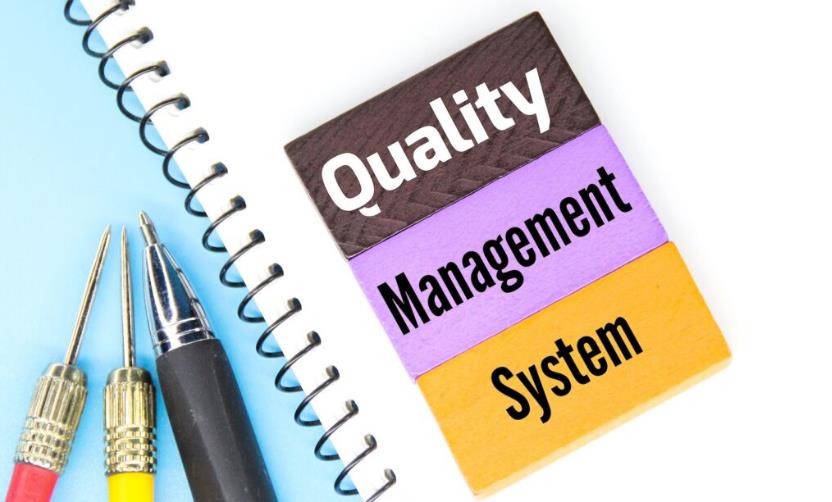
Chaotic management has a more significant impact on production efficiency and product quality.
The overall production process of air filters
The process of making air filters like cabin air filters and pleated filters is usually divided into below steps:
Choose air filter media
The choice of air filter media is the most critical link because the quality of the filter media is directly related to the quality of the whole air filter.
The filter factory will use the light inspection method to pass the qualified filter material through the light inspection device and check it carefully. The corresponding treatment should be applied if pinholes, glass slag, or foreign straw matter are found.
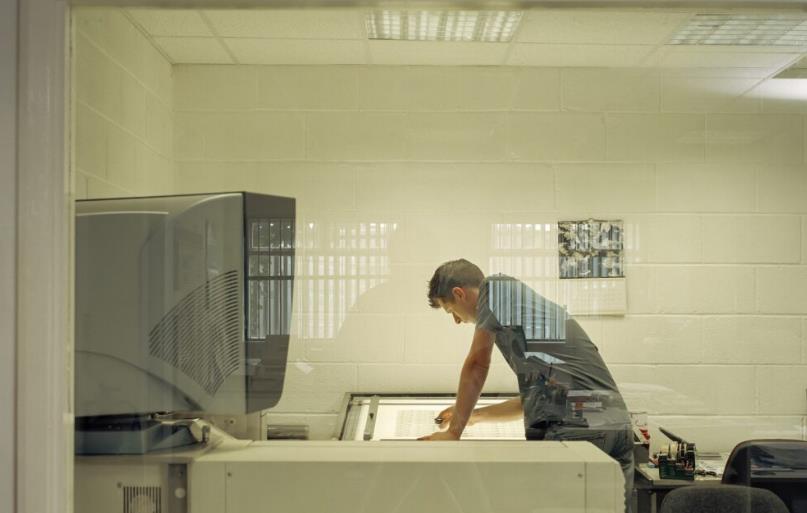
If there are broken filter materials, they should be cut off and connected with qualified filter materials.
Pleating
Nowadays, most filter factories have automatic pleating equipment, but each manufacturer’s process standard and parameter setting will differ.
The more professional manufacturers will set the pleat height, spacing, and other parameters according to the airflow, pressure drop, filter medium, and air filter information.
Other ordinary manufacturers do not necessarily have such technology.
Outer frame/housing production
Air filters with different filtration efficiency, size, and function usually have additional frame requirements, so it is necessary to determine the frame material and size according to the product requirements in advance and then make them accordingly.
Assembling
Assembling the pleated filter media and the outer frame is a complicated part, which has to be done with related equipment according to different filter and frame materials.
Sealing
It means that after the filter media and frame are assembled, the filter media and frame are sealed with sealant to produce no leakage to ensure the filtration accuracy and effect.
Sealing is essential for HEPA filters.
The last is the finished product testing. Most manufacturers will use the particle counting method or smoke test to detect whether the product is leaking and whether the filtration efficiency meets the requirements.
HEPA filter manufacturing
The production process of HEPA air filters needs to be very careful because whether the production process of the filter is delicate determines the excellent or lousy purification effect of HEPA air filters.
So generally, there are special requirements for the production process of HEPA air filters.
The outer frame and filter media make up the HEPA filter.
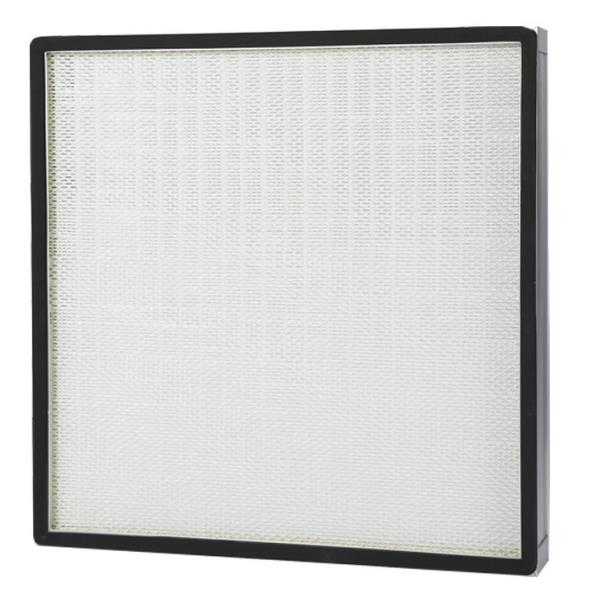
The production of the outer frame, initial inspection of filter media, re-inspection, filter media pleating, filter media insertion, glue sealing, and molding process are the necessary steps for processing and assembling high-efficiency air filters.
The following is a specific description of the production of high-efficiency particulate air filters.
Outer frame making
HEPA air filters require non-standard customization. Customers need different materials for the outer frame of HEPA filters, so the cost is also additional.
There are two standard frames: galvanized steel frame and aluminum frame.
To do the bending and bending angle of the outer frame according to the customer’s requirements, remove the excess processing burrs, and do the sealing treatment of the joints.
Frame cleaning: After making the frame, remove the oil stains and wipe them again to clear the dust and dirt on the frame.
Initial inspection of incoming filter media
Before unpacking the filter media, check whether the packaging and filter media are damaged after unpacking.
Check the product quality inspection and verification, especially the ultra-fine glass fiber filter media, and check more carefully.
Inspection with light
The light inspection process in air filter paper is different for deep pleat HEPA filters and mini pleat HEPA filters.
Light inspection occurs when the deep pleat HEPA filter paper is inserted into the forming process.
The mini pleat HEPA filter paper should be under light tested before it is fed into the pleating machine to see if it’s good.
Sealing
Seal the HEPA filter with sealant.
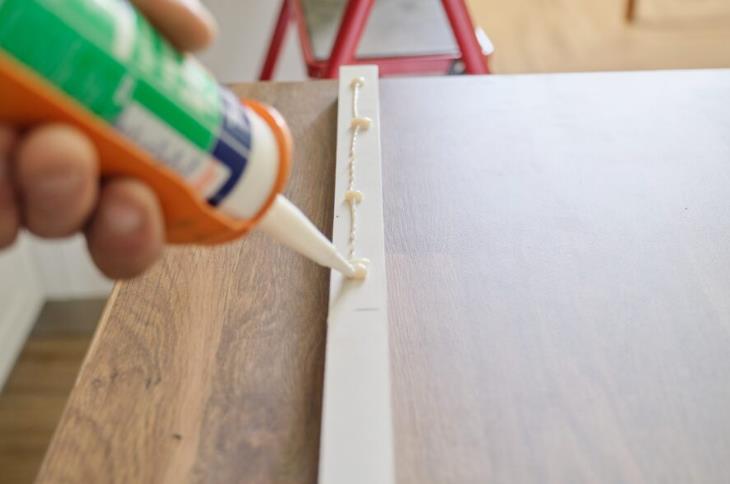
After sealing, wait for the sealant to cure, shovel away the cured overflowing sealant, wipe the outer frame of the filter with anhydrous alcohol, clean the filter, and then paste the rubber seal on the windward side of the outer frame of the filter.
Inspection
After completing the production process of the HEPA filter, the inspection can be carried out. Examining the HEPA filter includes efficiency, resistance, geometric size, end face flatness, side plate flatness, side plate unevenness, etc.
Among them, leak detection is the key to ensuring the quality of high-efficiency particulate air filters.
The production process of air filter cotton
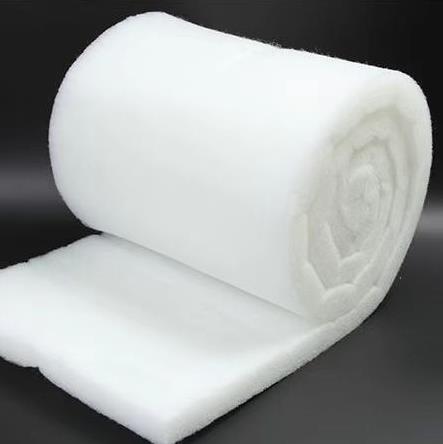
In the present life, many people are not unfamiliar with filter cotton or air filter cotton, and even many people at home are using this stuff. In this article, I bring filter cotton’s production process so that we know more about filter cotton.
Cotton blend
According to the different requirements of different customers, and then by different ratios to proportion different fiber cotton, first, weigh the initial weight, and then poured into the mixer by the machine rotation mixing, so that the purpose is to mix a variety of raw materials evenly.
Loosen
Some machines spread the stirred fiber mass evenly, and the fiber mass is transferred to the felting roller device. Then the fan sends the fiber mass after a strong opening and loosening to the second loosening and feeding device.
The fan sends the fiber mass to the blending box after the second loosening, and the vibration of the wool hopper does the blending.
Combing
Some special machines make the cotton dough thick and thin, transfer the evenly distributed cotton layer to another device, and lay it into a mesh.
Laying the mesh
A device swings back and forth several times, and the cotton layer becomes a uniform mesh before being placed in the oven.
Hot air setting
Send the Uniform layer of cotton to the oven. According to the principle of physics, the cotton layer is at a specific temperature in the oven. Various fibers hold together when it reaches a low melting point, forming synthetic fiber cotton.
Cold air shaping, edge cutting, and curling
After forming the synthetic fiber filter cotton, it will be shaped by cold air, then the thickness is determined by pressing the shaft, and finally, it is cut by the specified value.
When it is found that the length has reached the specified value, then the filter cotton is cut and then formed into a roll.
Air filter design and manufacturing
In general, air filters are designed and manufactured based on three aspects:
- The object to be protected.
- The standard to be implemented.
- The specific application.
Different air filters protect various objects.
Automotive Air Filter
Air intake filters protect intake system components for internal combustion engines, air compressors, and other machines.
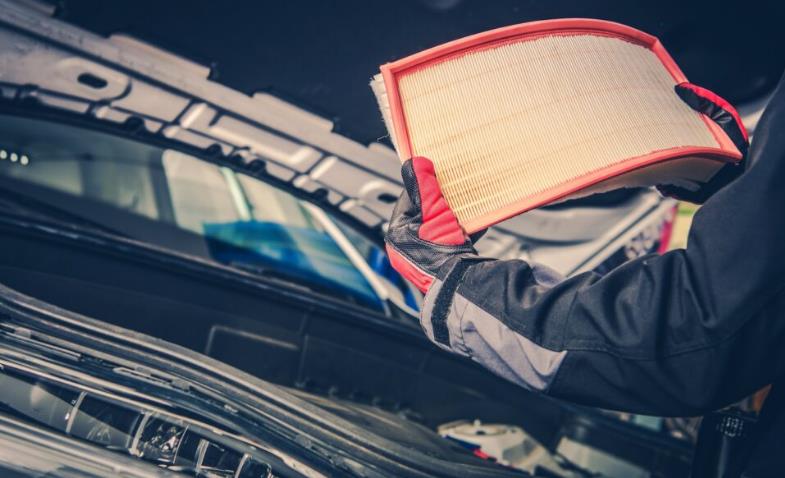
It is used in the intake air purification of engines of automobiles, various combat vehicles, various ships, railroad locomotives, aircraft, launch vehicles, etc.
Air filters for clean technology
Let the clean room be dust-free to ensure product quality, and the fume plant be cleaned to ensure a healthy environment.
Its application in the production workshop purification of drugs, food, and electronic products;
Museum, library, and other collections room purification:
Operating room, gymnasium, production plant fume emission;
Walking machine, flying machine, cockpit purification.
Atmospheric environmental protection air filter
These filter smoke and dust, protecting the earth.
Its application in cement plants, power plants, steel plants, etc., smoke and dust filtration;
also in waste incineration, coking and iron making, forging and casting plant, etc., fume and dust filtration.
After understanding the object to be protected, experienced air filter manufacturers will know what kind of filters to produce to meet the requirements.
Standards implemented in different countries for air filters
- European Standard: EN779 Determination of efficiency by gravimetric method
- European standard: EN1882 particle size penetration method to determine the efficiency
- American Standard: ANSI/ASHRAE 52.2 Determination of filtration efficiency by gravimetric/counting method
- China Standard: GB12218 Test Method for Atmospheric Dust Filtration Efficiency
- China Standard: GB6165 Sodium flame method for the Determination of filtration efficiency
Air Filter factories should be familiar with these standards and differences to produce air filters that meet different standards accurately.
Air filters in clean room applications
Ultra-clean clean room
Ultra-clean clean rooms are used in pharmaceuticals, particle size tests, biological research, special wards, electronic chip production, etc.
Most of these ultra-clean rooms use high-efficiency (HEPA) filter material with 99.97% efficiency, and even ultra-high efficiency (ULPA) filters with 99.999% efficiency.
There is also the use of colorimetric method efficiency 90% ~ 95% filter material.
General clean rooms
Per filtration efficiencies in general clean rooms as below:
- Electronic industry product assembly, testing, and research. Using HEPA filter material (99.97% efficiency)
- Medical: Operating room, ward, I.V. room. Filtration efficiency: 95% efficiency by gravimetric method.
- Pharmaceutical: workshop, packaging room. Filtration efficiency 95%, 99.97%.
- Museum: the collection of cultural relics, winter book storage, identification and testing, and restoration of cultural relics. 95% efficiency by gravimetric method.
- Chemical fiber production: drawing workshop, textile production room. Particle counting method, 95% efficiency.
- Food processing: production workshop, packaging line. 95% efficiency by gravimetric method.
- Industrial oil purification: filter evaluation, oil contamination test. High-efficiency filtration HEPA.
- Automotive industry: car paint line, electrostatic spraying line, painting line. 95% efficiency by gravimetric method.
- Nuclear power plant: exhaust system, use HEPA filtration.
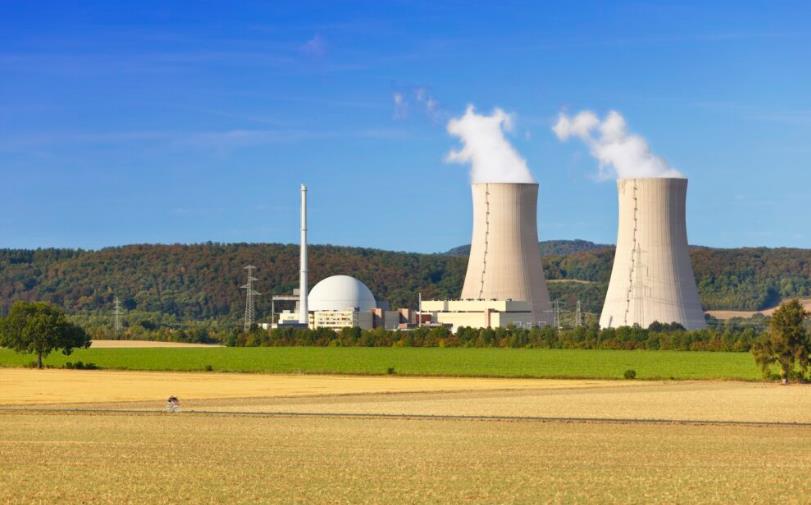
- Infant protection: Hospital infant nursing room, kindergarten activity room. 90% efficiency by gravimetric method.
- Memorial hall: statue room of great people, room for viewing the remains of great people. 90% efficiency by gravimetric method.
- Tobacco industry: production workshops, packaging lines. 95% efficiency by gravimetric method.
- Metallurgy: motor room of rolling workshop, electric control room. 95% efficiency by gravimetric method.
- Airports: terminal protection. Lounge protection. 95% efficiency by gravimetric method.
- Dairy industry: the original milk pulp purification workshop, steaming line. 95% efficiency by gravimetric method.
- Air conditioning: general air conditioning systems. High-grade cinema theater and concert hall. 95% efficiency by gravimetric method.
- Personal protection: anti-drug masks, aircraft cockpit decontamination, cockpit dust control, car dust control. 90% efficiency by gravimetric method and HEPA filtration level.
- Air shower room: personal decontamination of operators before entering the above clean areas, using HEPA filtration.
In human production and life, there are many occasions when clean air is needed, yet the required degree of cleanliness varies.
This results in different shapes of air filters, various sizes of filter particles, and different materials are chosen for filtration.
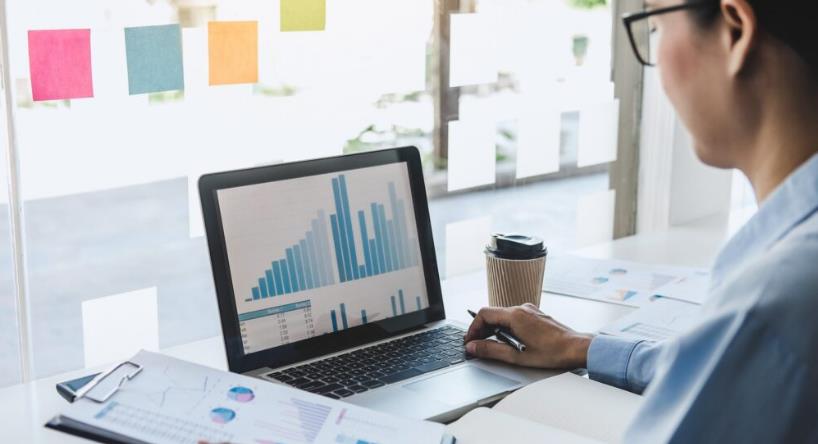
As a professional air filter factory, we are very familiar with the air filtration standards of various industries, air filter products, and air filtration technology. We can help you realize any air filtration needs.