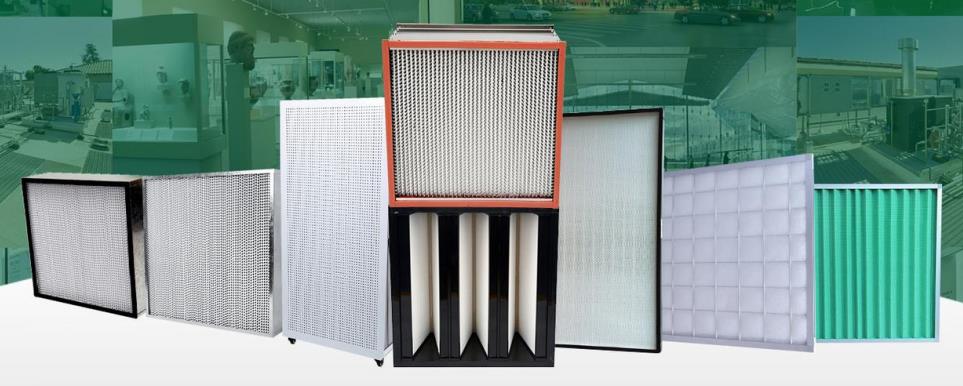
The air filters that can achieve the filtering purpose and requirements are the best, which must be analyzed and judged from many application scenarios.
On the other hand, the evaluation of the air filters is mainly from 2 aspects to judge, one is the quality of the air filters, and two is whether the air filters with the application scenario match.
The following factors influence the quality of the air filters.
Air filter material and production process
A good air filter will use high-quality filtration materials and be completed by precise processing technology. It has good mechanical performance, filtration efficiency, and cleanliness.
It can effectively trap airborne particles and improve indoor air quality.
Life of the air filter
As the filter accumulates dust, the air filter’s resistance increases in the use process. When the resistance increases to a specific value, the filter is scrapped, and the filter’s life ends. At this time, it is a must to replace the filter with a new one.
And the factors that affect the resistance of the filter are
The resistance of the filter material
The greater the resistance of the filter material, the greater the resistance of the air filter.
Filter area of the air filter
The larger the air filter area, the lower the resistance.
Cleanliness of the application scene
The more pollutants in the filter’s working environment, the more particles and dust the air filter accumulates per unit of time and the higher the resistance. The shorter the life of the filter will be
Air velocity
The higher the airspeed, the higher the resistance of the filter.
Basic quality standards of air filters
Air filters will be produced following the drawings and technical documents approved by the prescribed procedures.
Appearance
- The surface of the filter frame is free of apparent contaminants, dents, scars, and damage.
- There is no damage to the filter media and separator.
- The sealant is neat and free of cracks.
The allowable values of deviation of external dimensions are as follows:
Side length
For side lengths greater than 500 mm, the deviation is 0-3. 2 mm.
If the side length is less than or equal to 500 mm, the deviation is 0-1. 6 mm.
Depth
The deviation of the depth dimension is 0-1.6 mm.
Diagonal
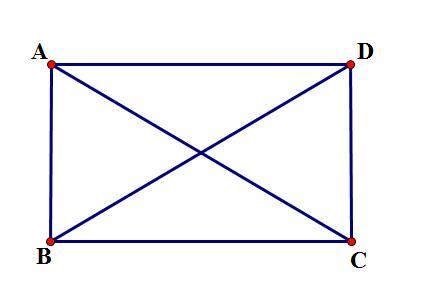
The tolerance of the two diagonals of each end face of the air filter is mentioned here.
When the diagonal length is more significant than 700 mm, the tolerance should be less than or equal to 4. 5 mm; when the diagonal size is less than or equal to 700 mm, the deviation should be less than or equal to 2. 3 mm.
Perpendicularity
The air filter’s frame end and side should be vertical.
Flatness
The flatness of the air filter end face and side should not be greater than 1.6 mm; the deviation of parallelism of the two end faces should be less than or equal to 1.6 mm.
Filter materials
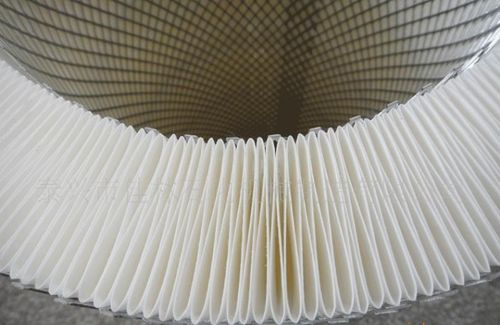
- Permeability and resistance performance should meet the performance requirements of filters of the same filtration level.
- Tensile strength:longitudinal not less than 0. 30 kN/m, transverse not less than 0. 20 kN/m;
- The thickness should be uniform, the filter media should not contain hard lumps, and the surface should not have cracks, abrasions, pinholes, color spots, etc.
Adhesive and sealant
The shear strength and tensile strength of the adhesive should be higher than the strength of the filter material.
The sealant should ensure that the filter does not crack, does not delaminate, and is elastic when the filter resistance reaches ten times the initial resistance in operation.
Basic quality standards of HEPA filters
HEPA air filters are of general interest among all filters because they have the highest filtration efficiency, can trap the smallest filter particle size, and are essential in many critical filtration systems.
Packaging
The outer packaging is intact and undamaged, with no signs of cracking.
The product model, air volume, airflow direction, and other markings should be complete, accurate, and complete.
Frame
- It has no obvious contamination on the surface of the frame of the HEPA filter.
And no dents, scars, scratches, coatings, flaking, burrs, or rust spots.
- The frame of the HEPA filter should be flat and without apparent deviation;
- The strength of the HEPA filter frame should meet the requirements. Put on a flat surface and shake, with no deformation or shaking of the structure.
Seams
The seal between the HEPA filter media and the frame should be tight, without gaps and holes.
The sealing gasket of the HEPA filter should be complete, without fracture, and visually flat.
The thickness of the sealing gasket should not exceed 8 mm, and the compression rate should be twenty-five to thirty-five percent.
Filter media
Filter media should be no damage, no stain, no debris, no wrinkle, no glue, and no patch.
It has no apparent damage to the separator. It should be flush and even.
The sealant is neat and crack-free, and the relative height difference between the filter media and the separator is less than 5 mm.
There should be no cracks, bubbles, holes, or folds in the sealant paste of the frame and filter media.
In addition to the quality of the air filter, it is also essential that the air filter matches the application scenario.
Air filter application scenarios
With the improvement in living standards, people’s requirements for air quality are rising, and air filter application scenarios are becoming more and more.
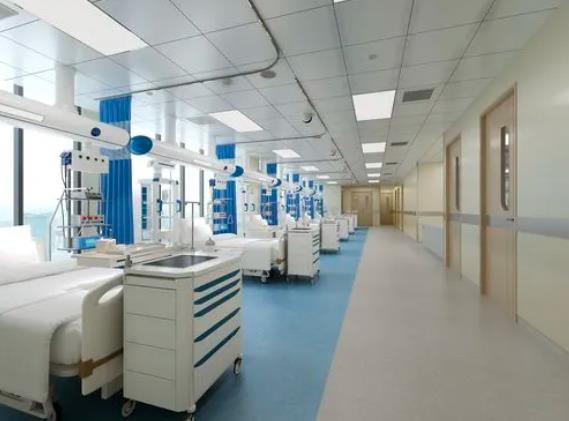
The most widely used scenarios for air filters are industrial manufacturing, hospitals, homes, and commercial buildings.
In industrial manufacturing, air filters have been widely used in air filtration in biological, semiconductor, pharmaceutical, food, beverage, cosmetic, automotive, precision instrument, pharmaceutical, and electronic industries that need the best air quality in their productions.
Whether it’s ensuring healthy and comfortable indoor air, creating a clean environment for production operations, or preventing hazardous substances from leaking, choosing the right air filter is critical.
Air filter application in industrial production
For factories such as food and beverage, cleanroom air filters are essential for air purification in clean rooms.
The presence of air filters can capture and adsorb dust particles of different particle sizes in the factory air to improve air quality and optimize the industrial production environment.
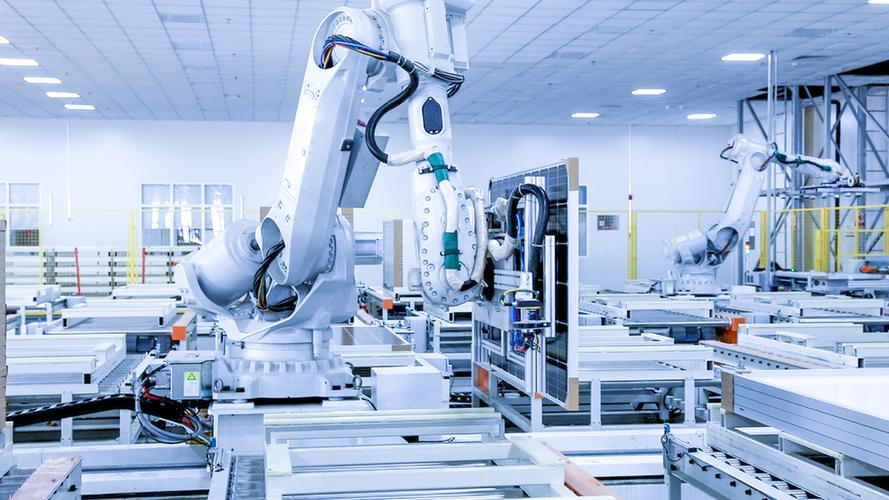
Of course, the air quality requirements vary significantly from factory to factory.
For example, in the semiconductor manufacturing and pharmaceutical industries, the air cleanliness requirements are high, so the workroom needs to be cleaned with a constant cycle of clean air filtered by HEPA filters.
In order to maintain the cleanliness and life of the HEPA filter, several sections of less efficient pre-filters are also required for everyday use.
For example, some factories equipped with fume hoods and pollution control equipment require a large amount of supplemental air. If the ambient air in the area where these factories are located is contaminated, then the supplemental air must be filtered before it is distributed to the workplace.
Air filter application in hospital
In addition to manufacturing plants, hospitals are also where air filters are used more often.
As we know, the health industry is vast and unique, which also requires high air cleanliness.
In general, HEPA filters are not required, but in exceptional cases, such as isolation rooms and specific testing and care areas, high-efficiency particulate air filters are needed.
Air filter application in homes and office buildings
In recent years, as people’s demand for quality of life is getting higher and higher and the growing number of allergy sufferers, some residences have started installing air filtration systems like residential HVAC systems and air purifiers.
Air filters are also widely used in HVAC systems in public buildings such as airports, stations, and office buildings.
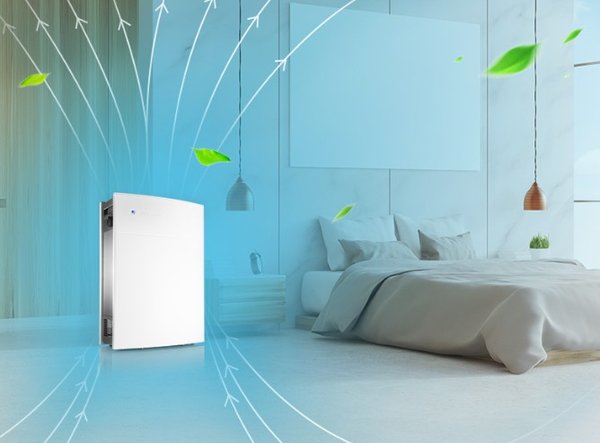
Activated carbon and medium and HEPA filters are often used in air purifiers in these locations to remove dust pollen, pet dander and pollen, airborne allergens, dust and lint, and smaller particles to clean the air.
What air filter is best for industrial production?
Many industrial productions will use high-efficiency filters, such as optical electronics, LCD liquid crystal manufacturing, biological medicine, precision instruments, beverage and food, PCB printing, and other industries at the end of the clean room air conditioning supply.
But there are many air filters; which air filter is the best for the industry? Let’s analyze it.
Determined by the production process of the plant
First of all, the selection is based on the product technology. Since the production process of various factories is different, the nature of the gases and dust in the workshop also differs.
The selection of HEPA filter media should be combined with the specific production process.
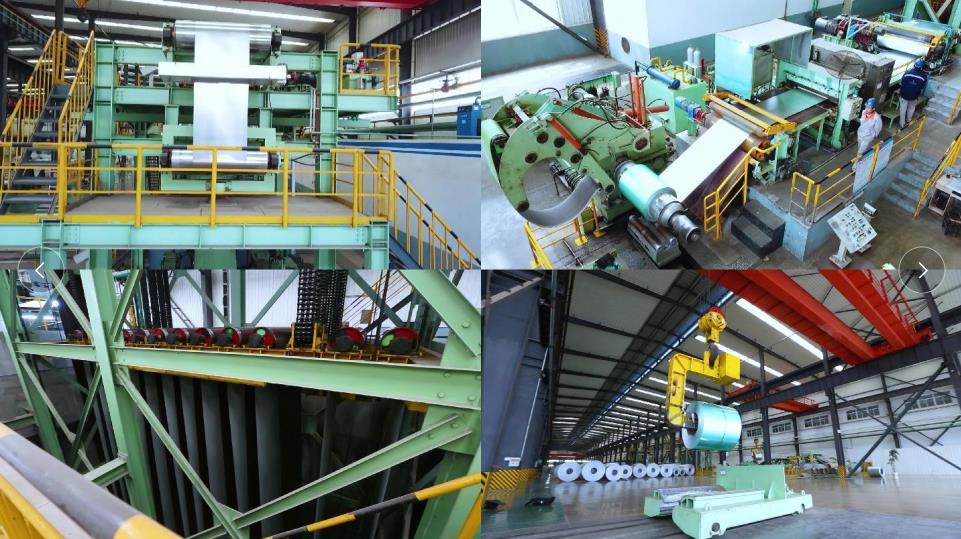
For example, if there is still a large amount of dust in the flue gas, the diameter of the dust particles is large, and the moisture content is low, the filter media with large air permeability and fabric structure should be used.
On the contrary, if the dust content in the flue gas is not high, the particles are fine, and at the same time, it is easy to bond; you should choose the woven filter media with smaller air permeability.
According to the characteristics of dusty gas
When using HEPA filters, the properties of the dust-containing gas should also be considered.
Generally speaking, the properties of dust-containing gases are judged by criteria such as temperature, humidity, chemical composition, and gas volume.
The temperature determines the air filter’s structure and the filter media choice.
The humidity affects the selection of the water repellency of the air filter, and the chemical composition should be considered to choose a suitable air filter without chemical corrosion.
Gas volume is the main factor in determining the size of the air filter.
According to the nature of the dust
The nature of the dust is mainly concentration, particle size, viscosity, and corrosion. These properties are also the main factors affecting the selection of air filters.
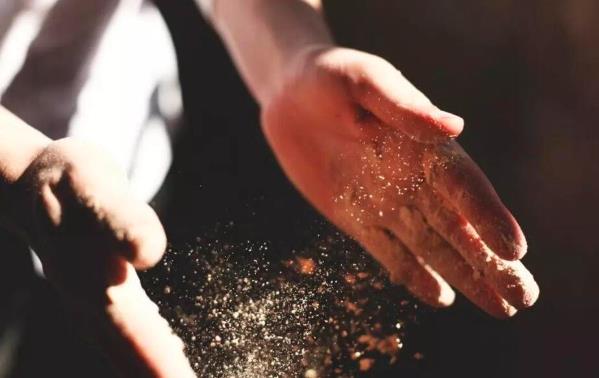
If the dust concentration is high, a lower filtration airspeed should be taken, and the negative pressure design and the capacity of ash storage and discharge should be considered;
When the dust concentration is low, a higher filtration airspeed should be selected appropriately.
When the dust concentration is very low, consider the positive pressure design.
The lower air inlet method should be prioritized for coarse-size dust.
An air filter with a clean surface should be used for dust with high viscosity.
What air filters are best for purification and air conditioning systems?
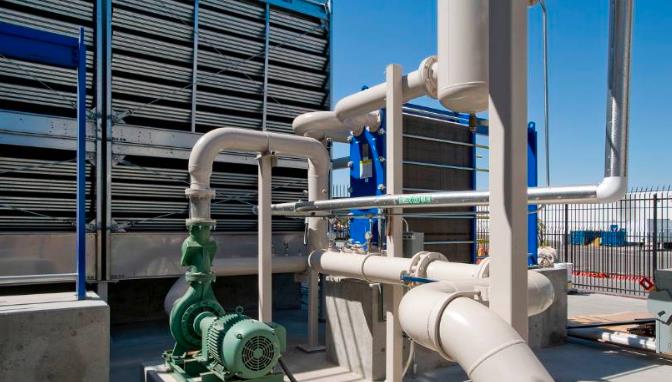
The air filter is the core component of a ventilation air conditioning system. The right air filter reduces the operating cost of an air conditioning system.
It is essential to use the filter’s service life fully.
Multi-level matching of filters
Usually, the end filter determines the level of air purification, and people tend to focus on the end filter.
However, the protection role of front air filters at all levels should be noticed, which protects the end HEPA filters to extend their service life and ensure the regular operation of the HVAC or air conditioning system.
- The pre-filters efficiency determines the end filter’s service life.
Clean air conditioning system design must be based on the user’s air cleanliness.
The efficiency of the terminal filter must be determined according to the user’s cleanliness requirements, and then the pre-filter must be selected.
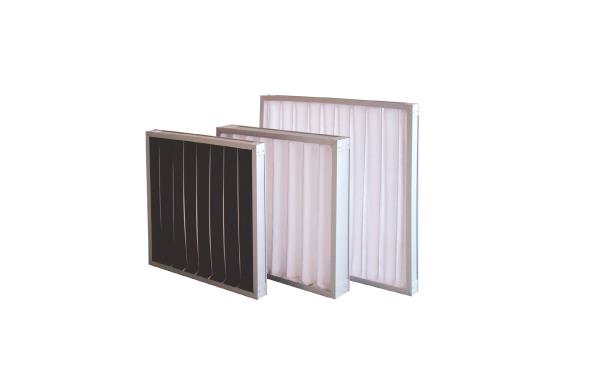
The selection of the pre-filter must take into account the efficiency match.
If the difference between the efficiency specifications of two adjacent filter stages is too significant, the first stage
can not protect the role of the next level.
If the difference between the two stages is slight, the burden of the latter stage is too small.
According to the European classification standard, when using the “G-F-H-U” efficiency classification, it is easy to estimate the efficiency of the required filter stages.
In G2-H12, a filter is set up every 2 to 4 levels.
For example G4, F8, H13. F8 protects H13, G4 protects F8, and if G3 is chosen, the life of F8 is greatly reduced.
The same setup as above can be applied to minimum efficiency reporting value ratings.
2. For air filters with the same construction, material, and final resistance, a 50% increase in air filter area increases the filter life by more than 70%.
A doubling of the air filter area increases the air filter life by three times.
When choosing a filter for a clean air conditioning system, it is essential to pay attention to the efficiency matching problem and the effective area of the filter.
Do not change the filter at will to save space.
Which is likely to cause the filter life to be reduced, the system resistance increases, and operating costs to increase.
Selecting the suitable filter efficiency
There are always some users who are worried that cleanliness cannot be achieved and repeatedly ask to improve the filter’s efficiency.
In fact, in the case of the same ventilation parameters, the cleanliness of the clean room will not be much difference between using the 99.9999% filter and the 99.97% filter.
Choosing a higher-efficiency filter will increase the initial investment and the operating cost.
For a non-unidirectional flow clean room, the average air speed is much lower than the dust diffusion speed, and the air supply only plays a dilution role.
Since there are relatively more operators in this type of clean room, and the amount of dust generated by the equipment and production process is also large, the filter’s efficiency is no longer a decisive factor for cleanliness.
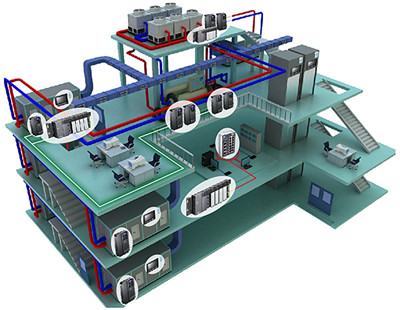
With the same ventilation parameters, the filter’s efficiency is influenced mainly by the size of the particles.
The selection of filters is mainly based on the production process requirements and the clean room level.
So taking all factors into account, among all the different air filter types, the most suitable air filter is the best.