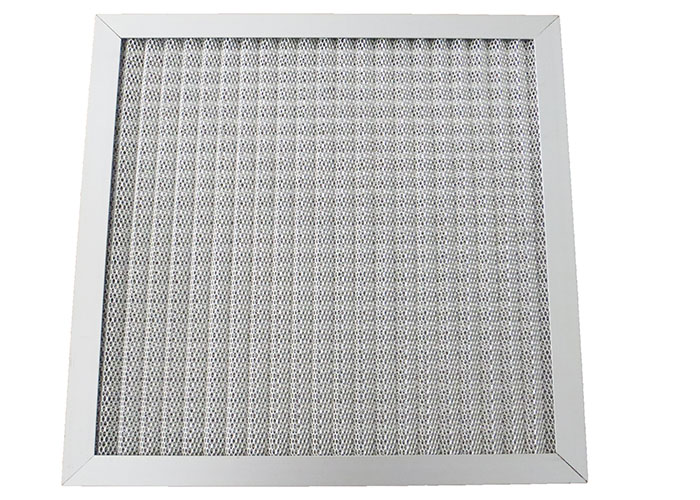
What is a metal mesh filter?
Metal mesh filters, referred to as metal filters, are made of metal wire mesh of different mesh sizes, which are used to filter the molten material flow and increase the resistance of the material flow to filter out mechanical impurities, oil mist, etc.
It also filters large particles in the air, mosquitoes, leaves, Oil pollution, etc.
It is acid-, alkali-, temperature- and wear-resistant and is mainly used in the mining, petroleum, chemical, food, pharmaceutical, and machinery manufacturing industries. It is also used in some ventilation or commercial HVAC systems as a pre-filter or basic filtration.
As quoted, it is widely installed in commercial HVAC equipment from Trane or York Inc.
Why need a metal mesh filter for some ventilation systems?
Do you need clarification about which filter to choose if the ventilation system is highly corrosive, has high temperatures, and is heavily contaminated with moisture and oil?
Metal mesh air filter solves all problems, and this filter can also be cleaned or washed, saving costs.
Metal mesh air filters are usually made of all aluminum and stainless steel but can also be made of a mixture of several metals.
How does a metal mesh filter make?
Multiple layers of expanded aluminum or stainless steel mesh are laminated into a wavy shape and cross-laminated at a designed angle.

Multiple mesh layers allow the air flow through the filter to change direction several times, increasing its dust collection capacity and efficiency.
Washable Metal Air Filters
Both aluminum and stainless steel mesh are safe, robust, high-temperature resistant, washable, and easy to clean and maintain.
Long-term recycling reduces the cost of use.
It has a low resistance, long service life can be washed repeatedly, and is cost-effective.
What are the characteristics of metal mesh air filters?
The metal air filter has multiple layers of metal mesh arranged in different densities and pore sizes from coarse to fine to achieve low resistance to airflow and increase its dust collection capacity and filtration efficiency.
- It’s washable, can be reused many times, has a long life, and can save costs.
- It consists of multiple layers of crosswise and longitudinal corrugated mesh to increase the filtration area more effectively.
For example:
Thickness: 25″ Average efficiency: 72.5% Dust collection capacity: 91g/ft2.
Thickness: 46″ Average efficiency: 81.5 % Dust collection capacity: 143g/ft2.
- Filtration efficiency is EN 799 level: G2 EUROVENT4/5 level: EU2.
- Average weight counting efficiency: 65%-70% (ASHRAE 52.1-1992).
- Pressure drop: (recommended) 200Pa-(max) 200Pa.
- Metal mesh filters are acid, alkali, and high-temperature resistant because of their metallic qualities and can withstand temperatures up to 300 degrees or above.
What does a metal mesh filter do?
Metal mesh filters can work in harsh environments.
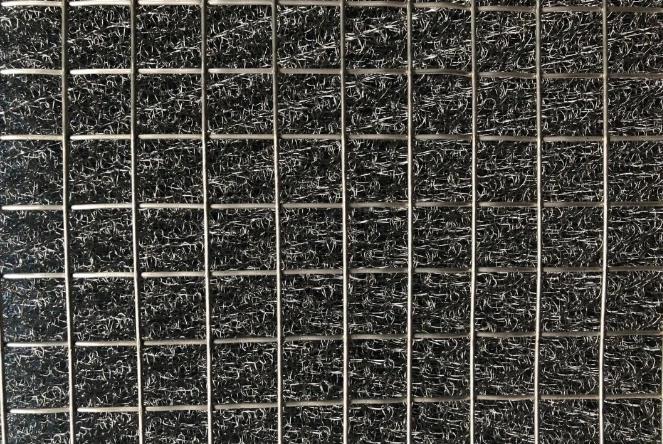
Metal filters are safe, washable, structurally stable, resistant to acids and alkalis, high temperatures, and humidity, and can work in harsh environments.
- For moisture and oil removal, primary filtration for harsh environments, and primary filtration for primary air conditioning systems.
- Coarse dust filtration for air conditioning in general buildings
- It’s used as pre-filtration for industrial air ventilation.
- They are used in ventilation systems that require acid and alkali resistance, high strength, and high-temperature resistance.
- Wax spray booth filtration in the automotive final assembly plant.
- They are also used in oil/grease separators and grease removers.
Filtering oil and fumes
The working principle of the mechanical filtration method to purify oil fumes is to make the smoke pass through the filter layer composed of a metal mesh filter and granular materials and adsorb the smoke particles through the filtering effect.
The mechanism includes collision, retention, and sieving according to the mechanical characteristics of particles.
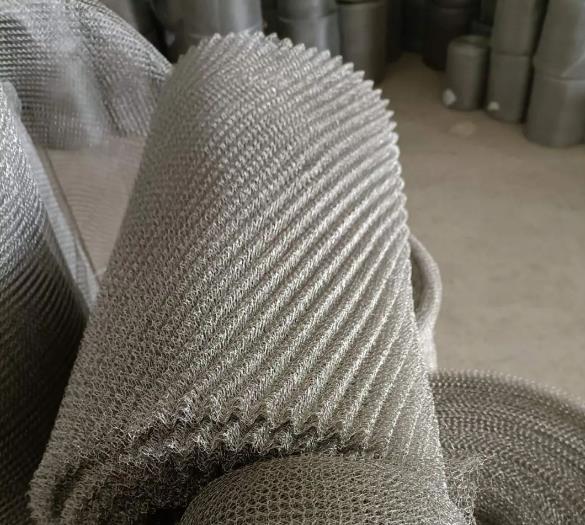
The oil fume purification equipment is made by the principle of filtration and adsorption, with a simple structure.
The metal filter’s density, thickness, and air velocity are the main factors that directly affect the oil removal efficiency and pressure loss.
This method is more efficient in cleaning oil particles but does not have any ability to remove malodorous substances.
Oil and grease have strong viscosity and adhesiveness, and it is difficult to achieve purification by gravity self-flow or squeeze removal.
Therefore, the washable metal mesh filter of the filter-type grease purifier needs to be cleaned and maintained frequently. Otherwise, it will affect the purification efficiency.
In fume control, metal mesh filters are used only as pretreatment, not as a separate control device.
Some indicators for evaluating metal mesh filters
Metal mesh filter as a filtration product, the primary assessment indexes include filtration accuracy, ash storage capacity, and pressure loss. Other assessment indexes also include the strength of the filter material, resistance to various media, heat resistance and heat resistance and other performance requirements.
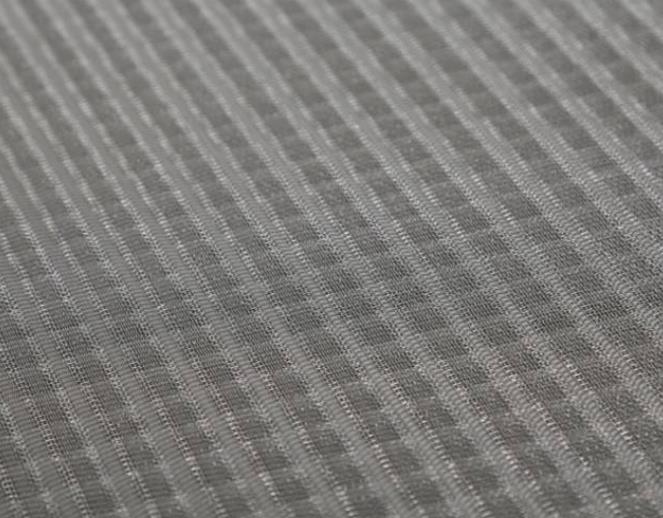
Metal filters, especially stainless steel filters, have the advantages of not easy corrosion, good stability, and high strength, so we mainly focus on the considerations in its filtration.
Filtration accuracy
Metal filters mainly rely on controlling the mesh pore size to achieve control of filtration accuracy. The smaller the mesh pore size, the higher the relative filtration accuracy.
Controlling the uniformity and stability of the mesh pores is the key to achieving the intended filtration efficiency and direction of the air stream.
The pore size is generally characterized by the size of the holes interwoven into the metal wire in mm, or the number of holes per square cm(mesh) is calculated.
The smaller the mesh pore size, the larger the value and the higher the filtration accuracy.
Dust storage capacity
The dust storage capacity is used to indicate the ability of a metal filter to store impurities.
The dust storage capacity value is generally defined during the test by continuously adding dust until the pressure rises to a certain level.
The test method shows that the dust storage capacity is a value related to the increase in pressure. The higher the pressure value after dust addition, the higher the dust storage capacity of the filter can be.
In some applications, maintenance replacement time is used instead of dust storage as a performance indicator, which has a similar meaning.
Metal mesh filter for Vapor-liquid separation
The metal wire used for vapor and liquid separation metal mesh filters is generally φ0.08~φ0.50 mm round or pressed flat wire. The wire diameter ≤φ0.30 mm can be multi-stranded knitting. Multi-stranded knitting can also be in metal and fiber wire together.
Common metal mesh material is stainless steel.
Principle of vapor-liquid separation
Droplets with a particle size of 100 microns or more can be easily separated because of their high settling speed.
Droplets with a diameter greater than 50 microns can be separated by gravitational sedimentation.
Droplets above 5 microns can be separated by inertial collision and centrifugal separation.
Droplets with a general diameter of 3 µm – 5 µm can be separated using a vapor-liquid metal mesh filter.
How does a metal mesh filter work in vapor-liquid separation?
First, the vapor liquid rises at a certain speed through the metal filter mesh erected on the grille. This metal mesh is the vapor-liquid filter, generally using stainless steel wire woven. The mesh size has 2*4mm, 4*5mm, 7*12mm, and so on. The mesh hole is so tiny to separate the liquid in the vapor better.
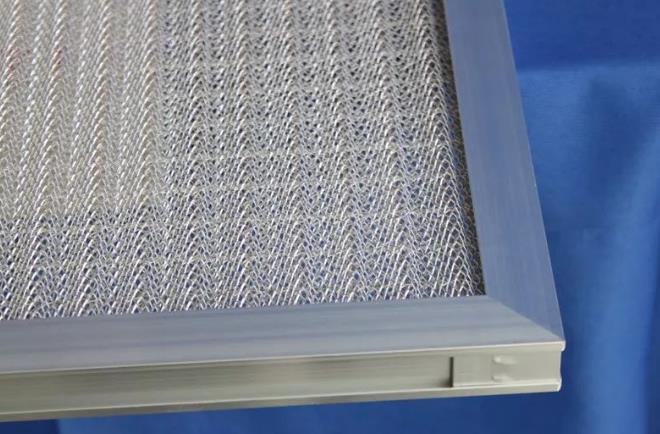
Then when the vapor collides with the stainless steel wire, the foam will adhere to the wire.
Then the liquid on the wire constantly gathers to form a larger liquid froth along the wire flow to its interweaving and finally form a larger droplet until its gravity exceeds the buoyancy of the gas rising and the combined force of the surface tension of the liquid.
The droplet will be separated and fall, flowing to the downstream equipment of the container, and the whole vapor-liquid separation process is over.