PAO testing is the primary method for leak test in clean room HEPA filters.
High-efficiency particulate air filters, known as HEPA filters, typically boast a collection efficiency exceeding 99.97% for particles sized 0.3 micrometers or larger. Employed as terminal filtration devices in cleanrooms, they ensure the provision of purified air.
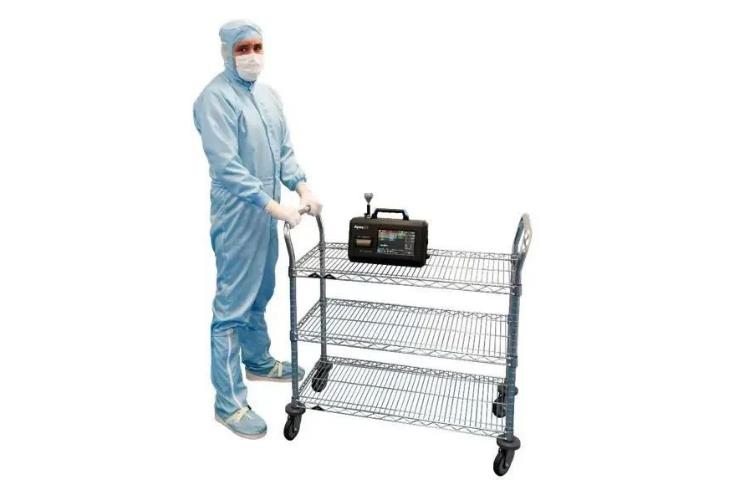
The attainment and sustenance of the designated cleanliness level in a cleanroom are correlated with the effectiveness of the HEPA filter and its installation. Therefore, conducting leak detection tests on HEPA filters in the cleanroom is one of the key means to ensure a clean environment in the workshop.
In pharmaceutical production, GMP and FDA also pointed out that a leak test should be performed after the HEPA filter is installed to check the sealing of the filter gasket, frame, filter material, etc.
Regular leak tests for HEPA filters are essential in sterile production workshops.
What is the purpose of the cleanroom HEPA filter leak test?
The manufacturer generally tests the filtration efficiency of the HEPA filter, and the test report and certificate of compliance are attached when leaving the factory.
For clean rooms, the HEPA filter leak test refers to on-site leak detection of HEPA filters and their systems after installation. It mainly checks for small pinholes and other damage in the filter material, such as frame seals, gasket seals, filter leaks in the structure, etc.

The purpose of leak detection is to detect defects promptly by checking the high-efficiency filter and its sealing with the installation frame and taking corresponding remedial measures to ensure the cleanliness of the area.
The principle of the PAO leak test
HEPA filter leak testing typically uses a DOP/PAO generator to generate an aerosol upstream of the HEPA filter. A photometer is then used to evaluate the aerosol concentration upstream and downstream of the HEPA filter to help identify potential leaks in the HEPA filter.
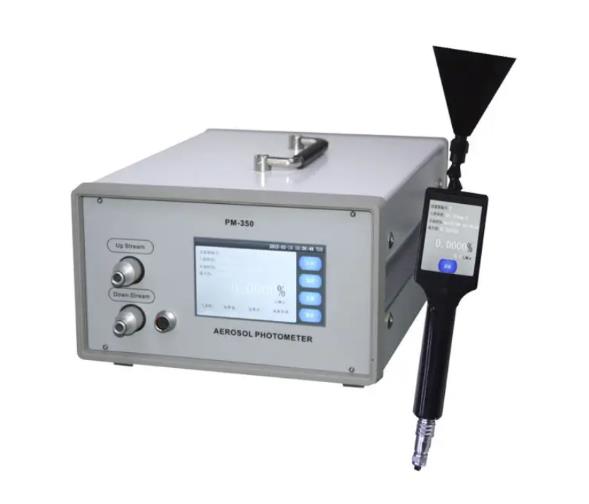
The purpose of dust generation is that due to the low concentration of dust particles upstream of the HEPA filter, it is difficult to detect leaks with only a particle counter without dust generation, and additional dust generation is required to clearly and easily detect leaks.
2 ways to generate PAO from the generator
There are 2 types of PAO generators: hot generation and cold generation.
The heat generator operates based on the principles of evaporation and condensation. The atomized aerosol particles are evaporated with a heater and condensed into tiny droplets under specific conditions. Upon eliminating excessively large or small droplets, a mist of 0.3um remains. PAO enters the air duct with a particle size distribution of 0.1 to 0.3um.
The cold generator uses compressed air to bubble bubbles in the liquid and splashes through the Laskin nozzle to produce polydispersed phase PAO aerosol in the physical state. The maximum distribution particle size is about 0.65um.
Cold PAO is often used when scanning HEPA filters for leaks.
Photometers and particle counters
There are two types of detection instruments: one is an aerosol photometer, and the other is a particle counter.
The commonly used detection instrument in HEPA filter leak detection is an aerosol photometer (hereinafter referred to as the photometer), a forward-scattered linear photometer.
It consists of a vacuum pump, a light scattering chamber, a photomultiplier tube, a signal processing converter, and a microprocessor.
As for the particle counter, its test value reflects the concentration of particles in the airflow. It also specifies the particle size range. Its high sensitivity applies to all dust source aerosols, and many choices exist. However, it is used sparingly in HEPA filter leak tests.
DOP and PAO
Artificial aerosol DOP has a history of nearly 40 years. For some time, it has been suspected of causing particular environmental pollution. It has been substituted with alternatives such as Dioctylsebaeate (DOS), also recognized as DEHS (di(2-ethyl hexyl)sebacate) and PAO (polyalphaolefin). Nonetheless, the experimental technique is still called the “DOP method.”
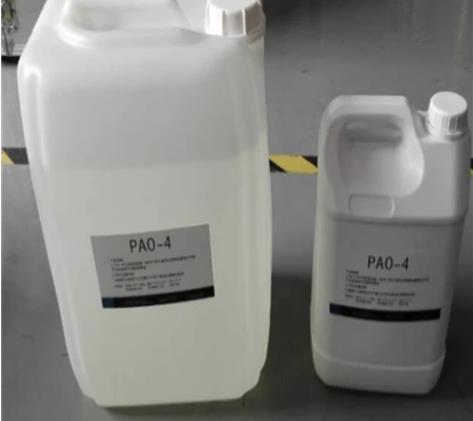
Since the concentration of atmospheric dust changes with location and time, sometimes it is more extensive and sometimes lower; it is not used for leak detection.
FDA points out that when conducting leak tests, the selected aerosols should meet specific physical and chemical requirements, and aerosols that can cause microbial contamination and breeding should not be used.
HEPA filter PAO leak test method
To determine whether there are apparent leaks in the HEPA filter itself and its installation, the following points must be tested on-site:
- The filter material.
- The seal between the filter material and its frame.
- The sealing gasket of the filter and the filter support frame.
- The support frame and the wall or ceiling.
The materials and instruments used for the PAO test include a dust source (PAO solvent), aerosol generator, and aerosol photometer.
It uses air directly without compressed air as power.
Test method
PAO aerosol is introduced on the upstream side of the HEPA to be tested.
For HEPA in the HVAC system, achieving uniform aerosol concentration at the filter requires the direct introduction of aerosol from the negative pressure side of the system fan.
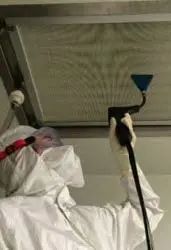
Suppose the introduction is to be done through the air duct. In that case, it is recommended to introduce it at a distance of at least 10 times the diameter of the air duct from the HEPA filter while minimizing turns, as per the American Society for Environmental Science and Technology.
Under normal circumstances, it is enough to keep the upstream aerosol to the required concentration and the concentration to fluctuate within a specific range.
For HEPA filters in laminar flow hoods and ultra-clean benches, aerosols are introduced directly from the negative pressure side of the system fan.
Initialize the aerosol photometer and set the 100% and 0% reference standard values according to the operating requirements of the aerosol photometer. Initialize and set the alarm value.
Attach the upstream sampling tube to the designated upstream sampling port and gauge the aerosol concentration in the upstream section.
Adjust the generated aerosol concentration according to the operating requirements of the aerosol generator so that the upstream aerosol concentration reaches 10~20ug/mL.
Scan for leaks
Remove the HEPA filter box’s diffuser and scan the seals on the entire filter surface, between the filter and the frame, between the frame and the frame, and between the frame and the static pressure box.
When scanning, the sampling head is about 1 inch (about 2.54cm) away from the HEPA filter’s surface, and the scanning speed does not exceed 5cm/s. Scan linearly in a back-and-forth motion, ensuring that the lines overlap.
Result judgment and processing
The leakage rate of the HEPA filter should be less than or equal to 0.01%.
If the HEPA’s %LEAKAGE (leakage rate) at all points does not exceed 0.01% during the testing process, the HEPA air filter will be judged to be qualified. If there is a % that exceeds 0.01%, it will be judged to be unqualified, and the point will be marked. It needs to be repaired or replaced.
Leak test cycle
The FDA recommends in the Sterile Production Guidelines that a leak test be conducted every six months for aseptic production workshops, and the GMP Inspection Guidelines recommend usually once a year.
ISO14644 recommends a maximum interval of 24 months for leak detection of installed HEPA. The DOP test should be performed after HEPA filter installation or replacement.
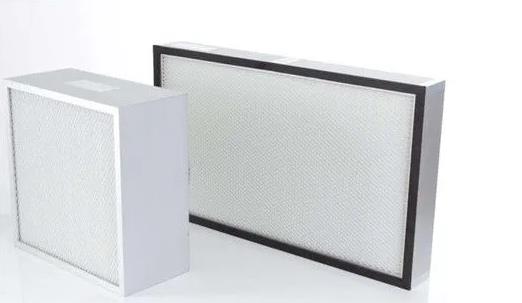
Leak detection can be performed as part of a deviation investigation when environmental monitoring shows deterioration in air quality or when a product fails a sterility test or a culture medium simulated filling test fails.
Air filters that need to be tested for leakage include HEPA filters used in drying tunnels and ovens.
One more discussion: Hepa filter efficiency and leak detection
The HEPA filter’s filtration efficiency refers to the filter’s efficiency, which varies with the standards and test methods implemented.
The current testing methods for the efficiency of HEPA filters include:
The DOP/PAO method, detected by a photometer, is less sensitive than the particle counting method. The relevant standards of this method can be found in the American IEST-RP-CC001.
The particle counting method uses a particle counter as a detection instrument and uses monodisperse or polydisperse aerosols. It has high sensitivity and is mostly used in ultra-high-efficiency filters. The relevant standards can be found in IEST-RP-CC007.
The most penetrating particle size method (MPPS) uses a particle counter as a detection instrument. The EU EN1822 standard stipulates this method. The difference from the particle counting method is that it uses the most easily penetrated by the filter as the particle size for testing.
Sodium flame method. This method uses a flame photometer to respond to the flame color of NaCL combustion. It has low sensitivity and is no longer used.
For pharmaceutical companies, the HEPA filter leak test is mainly an on-site leak test, and possible problems in the filter itself and the transportation and installation processes are discovered through the DOP/PAO method.
Aerosol photometers and polydisperse aerosols are often used because they are more economical and convenient than monodisperse aerosols and can meet the requirements.
Last thought
According to my experience, for the HEPA leak test of pharmaceutical companies, in the actual test, if there is leakage, the photometric count value will increase significantly, which is easy to judge. The leakage rate standard of HEPA filters is set to be less than or equal to 0.01%. It will not affect the detection of actual leaks.