High-Efficiency Particulate Air (HEPA) filters are critical components in environments that demand the highest levels of air cleanliness. This article delves into the meticulous process of manufacturing HEPA filters, highlighting the importance of raw materials, precise manufacturing techniques, rigorous testing, and stringent quality assurance measures.
Importance of Raw Materials
Selection of Filter Media
The foundation of a superior HEPA filter lies in the quality of its glass fiber filter media. Each roll undergoes comprehensive testing to ensure it meets specific parameters essential for optimal performance.
Critical Parameters Verified
To guarantee consistency and efficiency, the following parameters are meticulously assessed:
- Weight Fluctuation: Ensures uniform density across the media.
- DEHS Penetration at 0.3 µm: Evaluates the filter’s ability to capture sub-micron particles.
- Pressure Loss: Measures airflow resistance to maintain system efficiency.
- MPPS Penetration: Determines the most penetrating particle size efficiency.
- Water Repellence: Assesses durability in humid conditions.
- Thickness: Verifies uniformity for consistent filtration.
- Tensile Strength (Longitudinal and Transverse): Ensures structural integrity during handling and operation.
Precision Manufacturing Process
Clean Room Environment
Given the critical applications of HEPA filters, manufacturing occurs within an ISO 7 clean room to prevent any contamination of components or materials during production.
Pleating and Spacing Techniques
The filter media is pleated and separated using hot melt spacers applied from precisely calibrated nozzles. All nozzles are fed from a single tank to maintain consistent hot melt temperature and injection velocity, ensuring uniform mechanical characteristics across all spacers.
Bonding and Frame Construction
- Permanent Bonding: Pleated media packs are bonded to the filter frame using a bi-component sealant. Samples of the sealant are tested hourly to maintain bonding integrity.
- Frame Material: The frames are constructed from 20/10 extruded aluminum, providing high resistance to twisting and ensuring the filter’s structural stability.
Rigorous Testing Procedures
Compliance with Standards
Filters are automatically transferred to an ISO 5 testing clean room, where they undergo testing in accordance with the EN 1822 Standard. This process verifies both overall efficiency and MPPS efficiency at the rated airflow.
Testing Methodology
- Polydisperse Aerosol Challenge: A polydisperse aerosol is introduced to evaluate the filter’s performance across a range of particle sizes.
- Optical Particle Counting: An optical particle counter measures particle count and size distribution, providing detailed insight into filter efficiency.
- Downstream Sampling: A movable probe scans the entire cross-sectional area of the filter, including the frame, to detect any potential leaks or inefficiencies.
Detailed Test Reporting
Post-testing, an automatic testing machine generates a comprehensive report containing:
- Serial number and filter code
- Overall dimensions
- Filter medium type and MPPS value at corresponding velocity
- Test air conditions: temperature, relative humidity, and pressure
- Nominal airflow rate
- Challenge aerosol specifics
- Particle counter model, brand, and serial numbers
- Upstream particle concentration and dilution system
- Global and local MPPS efficiencies
- Filter classification according to standards
Quality Assurance Measures
Hourly Sealant Testing
To ensure consistent bonding quality, the bi-component sealant is sampled and tested every hour. This practice verifies properties such as curing time, adhesion strength, and chemical stability.
Consistency in Spacer Application
Maintaining uniform hot melt temperature and injection velocity is crucial. Regular calibration of nozzles and monitoring of the hot melt system prevent variations that could affect filter performance.
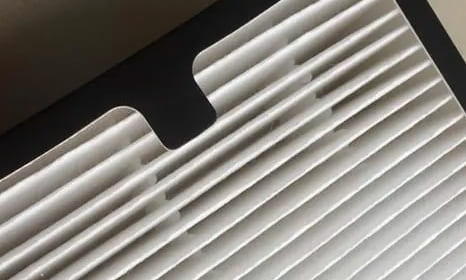
Labelling and Packaging
Comprehensive Labelling
Each filter is meticulously labelled with:
- Serial Number and Filter Type: For traceability and identification.
- Compliance Standards: Indicates conformity with standards like EN 1822.
- Filter Classification: Specifies the filter’s efficiency class.
- Nominal Airflow Rate: Denotes the airflow rate used for classification.
Protective Packaging
Filters are sealed in clean, protective plastic bags within the clean room to prevent any contamination after production. The individual test report accompanies each filter inside the packaging.
Final Boxing and Shipment
Sealed filters are carefully boxed, ensuring they remain pristine during transportation and reach the end-user ready for immediate installation.
Summary of Key Manufacturing Parameters
Parameter | Purpose |
---|---|
Weight Fluctuation | Ensures media consistency |
DEHS Penetration at 0.3 µm | Measures efficiency for sub-micron particles |
Pressure Loss | Affects airflow and energy efficiency |
MPPS Penetration | Identifies filter’s weakest filtration point |
Water Repellence | Enhances durability in humid environments |
Thickness | Contributes to uniform filtration performance |
Tensile Strength | Maintains structural integrity during use |
Conclusion
The manufacturing of HEPA filters is a precise and methodical process that prioritizes quality at every stage. From the careful selection and testing of raw materials to the controlled manufacturing environment and rigorous testing procedures, each step is designed to produce filters that meet the highest standards of air purity. Through stringent quality assurance measures and detailed documentation, manufacturers ensure that every filter performs reliably in critical applications, safeguarding environments that demand the utmost in air cleanliness.
As an experienced practitioner in air filter manufacturing, I can attest that attention to detail and adherence to stringent processes are paramount in producing HEPA filters that consistently meet industry demands.