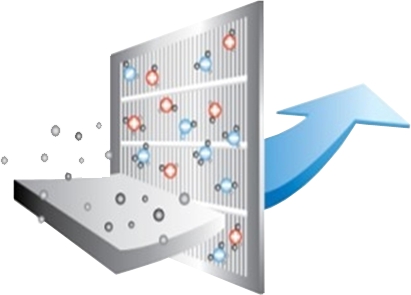
Air filter working principle
The adhesion force between dust and filter media
The dust particles in the air either make an inertial motion with the airflow, make an irregular motion, or move by some field force. When the particles in motion hit the air filter media, the van der Waals force between them and the air filter media makes them stick together. Above is the working principle of the air filter.
Air Filter media
Air filters treat all dust forms the same, whether particulate matter, solid, liquid, or bacterial.
The air filter material should be able to: effectively intercept dust particles without becoming excessive resistance to the airflow. Non-uniformly arranged fiber materials, such as various nonwoven fabrics or paper, meet this requirement. The interwoven fibers form numerous barriers to the dust, while the vast spaces between the fibers allow the airflow to pass smoothly.
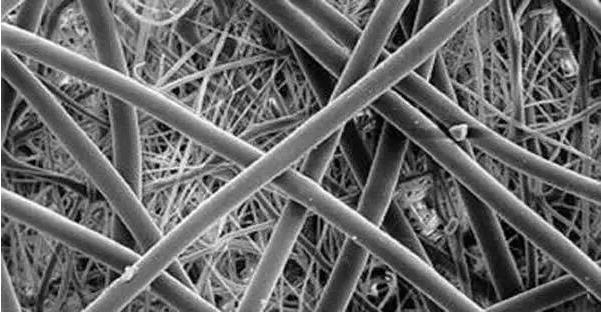
The widely used air filter materials are glass fiber, polypropylene fiber, polyester fiber, plant fiber, etc.
Air filtration Mechanism
Explained by the law of motion of the air filter media from the impact with dust, the common filtration mechanism is divided into the inertia principle, diffusion principle, and electrostatic force.
Airborne small particles of dust are mainly in Brownian motion. The smaller the particles, the higher the air filter’s efficiency; the larger the particles, the higher the air filter’s efficiency. Diffusion and inertia effects are not evident in that part of the dust is the most difficult to filter. For the air filter performance, the efficiency value of the lowest point of the air filter efficiency is the most representative.
Large particles of dust move inertially in the air stream. When the airflow meets the air filter material and goes around, the dust deviates from the airflow direction due to inertia and hits the air filter material.
The larger the particle, the stronger the inertia force, and the greater the possibility of hitting the air filter material, the better the filtering effect.
Tiny particles of dust are subjected to irregular Brownian motion. The smaller the dust, the more violent the irregular motion is, and the more chances it has to hit the air filter material, the better the filtering effect is.
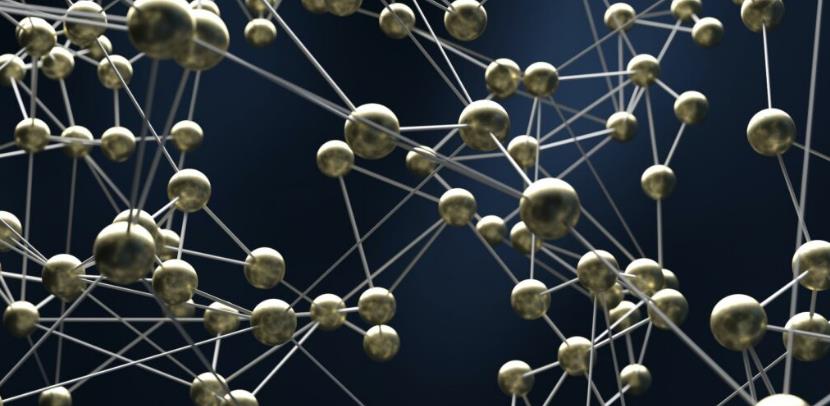
The filtration effect of the air filter can be significantly improved if the filter material is electrostatically charged or the dust is electrostatically charged.
There are two main reasons for this: the electrostatic force makes the dust change its trajectory and hit the air filter material; the electrostatic force makes the dust stick more firmly on the media. It has more and more applications in high-efficiency particulate air filters which are more effective in removing air particles, smaller particles, and other air pollutants.
And true HEPA filters are primarily electrostatic air filters. They use air filter media with static electricity to trap particles more firmly and remove smaller particles.
Air filter resistance
The captured dust creates additional resistance to the airflow, so the resistance of the air filter in use gradually increases.
The captured dust forms an additional obstacle by merging with the filter media, so the filtration efficiency of the filter in use will also increase.
Scrap the air filters when its pressure is too big
The captured dust mainly gathers on the windward side of the filter material. The larger the area of the filter material, the more dust it can hold and the longer the service life of the filter.
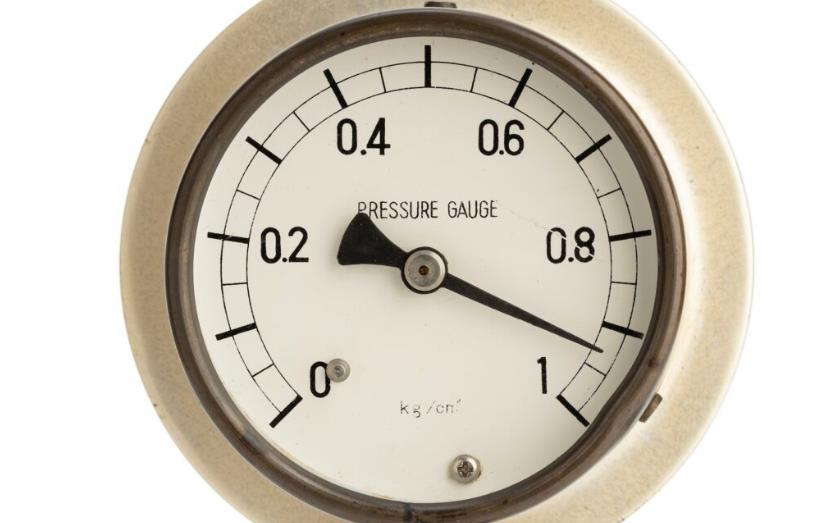
The more dust accumulates on the filter media, the higher the resistance. When the resistance is unreasonably high, the filter is scrapped.
Sometimes, the excessive resistance will cause the dust already captured on the filter to fly away, and when this danger occurs, the filter should also be scrapped.
Initial resistance and final resistance
Filter resistance increases with the airflow, and by increasing the area of the filter material, the relative air velocity through the filter material can be reduced to reduce the filter resistance.
The resistance of a new filter is the initial resistance, and the corresponding resistance at the end-of-life is the final resistance. The final resistance = 2 to 4 times the initial resistance.
Air filters’ Filtration principles
Airborne particles have a wide range of diameter distribution. Different filtration methods have been proposed for the nature of atmospheric particles in different environments, some for solid particles and some for liquid particles. However, all these filtration methods are based on the following basic filtration principles.
- Sieving or straining
- Settling or deposition
- Electrostatic precipitation
- Inertial separation
- Impingement/impaction (dry/viscous)
- Interception
- Diffusion
Sieving or straining
The sieving method is only suitable for removing lint (lint), hair, and other substantial particulate matter.
The principle is to use the spacing between the filter media fibers to screen out large particles by using a spacing smaller than the diameter of the particles.
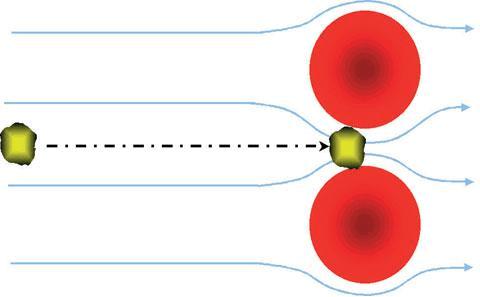
This principle is widely used in most filter designs and depends entirely on the size of the particle diameter, media spacing, and media density.
Settling or deposition
The settling principle is to use the particle’s gravity in the flow process gradually fall and separate from the airflow.
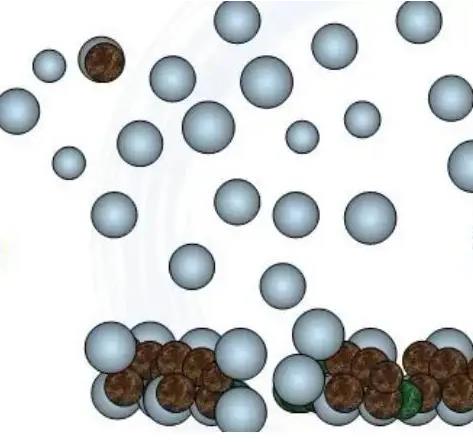
This principle is only suitable for separating particles with larger sizes, and the airflow speed is relatively slow.
Electrostatic precipitation
Electrostatic dust collection involves passing a high voltage direct current through two metal anodes and cathodes with a significant difference in radius of curvature to maintain an electrostatic field sufficient to ionize the gas.
The electrons, anions, and cations generated by the ionization of the gas are adsorbed on the dust passing through the electric field, and the dust acquires an electric charge.
The charged dust is deposited on the electrode by moving towards the electrode of opposite polarity under the electric field’s action to separate dust and air.
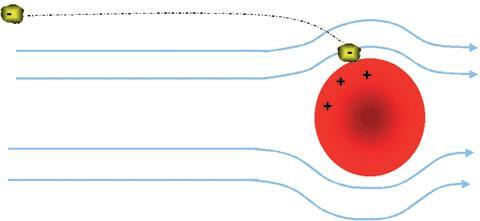
When the dust deposited on the electrode reaches a certain thickness, the dust falls into the lower dust hopper with the help of a vibrating mechanism.
It is worth noting that there are also filters that adsorb particulate matter in the air by charging the fibers of the filter media with a particular electrostatic charge and using the electrostatic force of the electrostatic charge on the particles.
Inertial separation
Inertial separation mainly uses the inertial effect of particles and the sudden change in the direction of airflow velocity to achieve particle separation.
Microparticles at a certain velocity maintain that velocity and keep going in the same direction. They will collide with the filter material under inertia and be captured.
If the concentration of particles to be filtered is very high, this filtration principle is generally used.
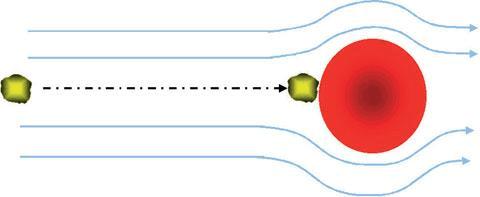
This method has a high separation efficiency when the particle diameter exceeds 10um and a low separation efficiency when the particle diameter is less than 5um.
Therefore, this filtration method can prevent erosion but not fouling when used in gas turbines. To make the particles have large inertia, this method requires the particle velocity to be around 3~6m/s.
We have made full use of inertia separation in the development of combustion engine filters. For example, the inertia principle removes sand and dust from the air. And in many cases, pre-filter models and more efficient end filters use this principle.
Impingement/impaction (dry/viscous)
Impulse separation is the use of particle inertia in the flow process and the filter fiber collision and then attached to the fiber to filter the air.
This method has high separation efficiency when the particle diameter is greater than 10um and only medium separation efficiency when the particle diameter is less than 5um.
This filtration method prevents erosion and reduces the fouling of gas turbine blades but does not entirely prevent fouling. We usually use this filtration principle to make pre-filters for gas turbines.
Using the impact separation principle, we have also developed a special viscous oil that is applied to the filter fibers to enhance the adhesion of particles to the filter fibers.
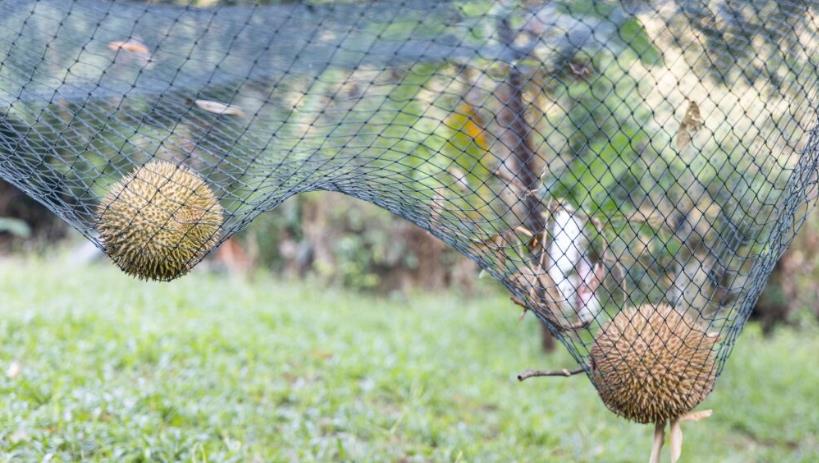
This viscous filter has a solid ability to adsorb particles and a greater dust-holding capacity. To ensure maximum impact separation particle efficiency, in addition to the use of viscous oil, the filter media fibers are usually required to be as large in diameter and as numerous as possible to allow sufficient airflow deflection to occur.
At the same time, the airflow speed is required to be 1.5~3m/s. This speed can ensure the particles have large inertia to avoid deflection when the particles go around the filter fibers with the airflow.
Interception
Interception separation uses the molecular attraction between tiny particles and between the particles and the filter media fibers to cause the particles to adhere to the filter media fibers.
In order to achieve interception, a particle must enter from within a radius distance of the fiber.
The particles thus come into contact with the fibers and adhere to them.
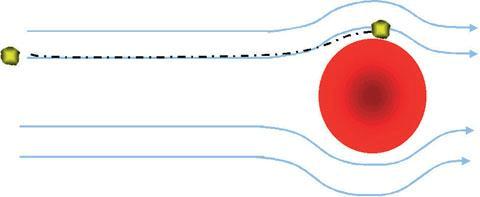
The difference between the interception principle and the embedding principle is that the intercepted particles are smaller, and their inertia is insufficient to keep the particles running straight. Therefore, they flow with the air until they come into contact with the fibers.
This method is more effective for particles with less inertia, the direction of particle movement can change with the direction of airflow, and particles are readily adsorbed on the fibers by molecular attraction when they flow around the filter media fibers.
This method requires a large filter media density and airflow velocity between 0.1~0.2m/s.
Diffusion
When the particles are extremely small, they will follow the random Brownian motion of the air molecules, and the smaller the particles, the stronger this random motion will be.
Diffusion separation takes advantage of this property by adsorbing the particles to the media fibers through molecular forces between the media fibers and the particles, i.e., van der Waal forces.
In order to enhance the diffusion separation effect, a high-density filter media is usually required, and the airflow velocity through the filter media should be very low (usually around 0.02m/s).
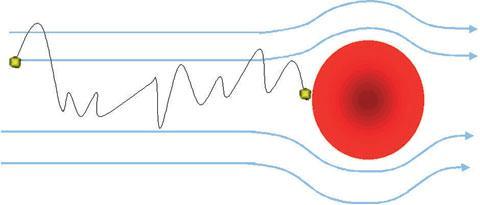
High-density filter media can increase the residence time of tiny particles in the filter media, on the one hand, so that those small particles can be fully diffused, and on the other hand, increase the chance of adsorption of particles by the filter fibers.
Most of the particles in the air are sub-micron size, so people usually use the principle of diffusion separation to make medium and high-efficiency filters.
Filtration principles to make air filters
The above description shows that different filtration principles exist for different sizes and properties of atmospheric particles. Therefore people usually need to use these filtration principles simultaneously to develop filters that can effectively filter air.
Combining these filtration principles to create a filter has different filtration efficiency for particles of various sizes.
When the particle diameter is greater than 1um, the separation effect of impulse and interception is better; when the particle diameter is less than 0.1um, the separation effect of diffusion is better. And the overall impact of diffusion separation and interception separation is lower for particles in the region of 0.1~1.0um.
Filtration system
In order to improve the overall filtration efficiency, people often use different filtration principles to create types of air filters of varying precision and then use these filters together as a filtration system.
Such a filtration system can achieve the best effect widely used in portable air cleaners, HVAC equipment, and ventilation systems to remove larger particles, indoor pollutants, and harmful particles in both industrial and commercial sites.
Activated carbon air filters, pleated air filters, HEPA filters, and primary filters form filtration systems in air purifiers to remove mold spores, gaseous pollutants, volatile organic compounds, dust mites, pet dander, animal dander, and dust particle to improve indoor air quality in residential spaces.
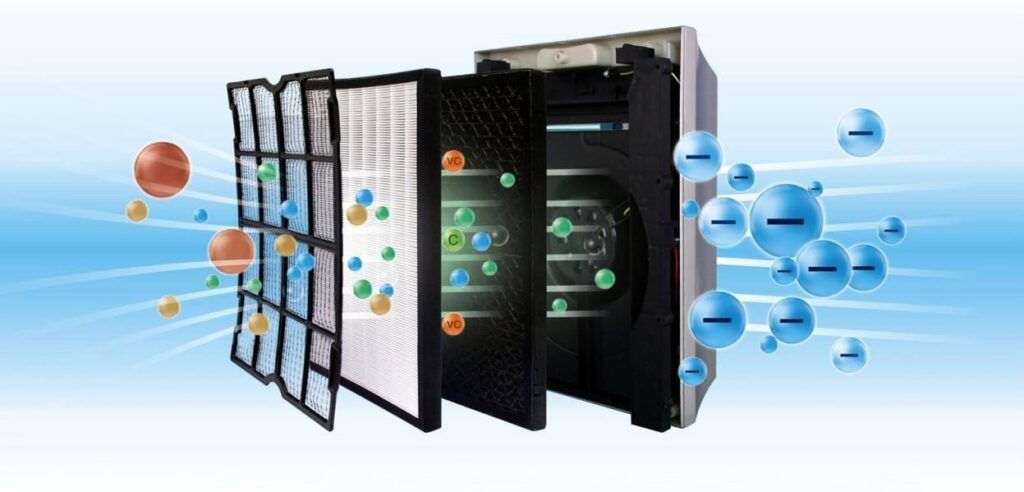
People have also invented Rating systems for air filter efficiency, such as the MERV rating system, which can help air conditioning engineers or buyers determine what filter is needed in the filtration process, HVAC system, or ventilation system.
Primary air filters
Firstly, collision separation (to enhance the adsorption ability of the fiber to the particles, the filter fiber can be with a viscous agent) to remove the large particles above 3~100um. The minimum efficiency reporting value is 1-4 for these primary air filters. They are reusable filters if well maintained.
Medium Efficiency air filters
Then use the interception and diffusion separation (using air filters with larger filter areas to increase the time of the particles through the filter media to enhance the filtration effect) to remove the particles in the range of 0.3~3um. These air filters are in higher Merv rating.
HEPA air filters
Finally, the particles in the range of 0.3um and below are entirely removed by diffusion separation (using a filter with a larger filter area to increase further the residence time of the particles in the filter media). Usually, these air filters are called HEPA filters. And most HEPA filters are disposable air filters.
With these types of air filters, people can improve air quality and get clean air in their life or workplaces.