From my experience, many purchasers, distributors, or end-users know that glass fiber filter paper is the primary raw material for HEPA filters. This is primarily because glass fibers have a small diameter, high filtration efficiency, and large dust-holding capacity. In this article, I will elaborate on several critical points about glass fibers in air filter paper to help people better understand this material.
What is glass fiber?
Glass fiber is an inorganic fiber whose main component is SiO2.
It is made by melting the glass frit at a temperature of 1300-1600°C, drawing it from the molten state and quickly quenching it. The diameter of the single filament ranges from a few microns to more than 20 microns. Equivalent to 1/20-1/5 of a hair.

Each fiber strand is composed of hundreds or even thousands of individual filaments. Its specific gravity is 2.54g/cm3, and the raw fiber tensile strength is 160~275kg/mm2.
In the following section, let’s look at 6 essential knowledge about glass fiber for filtration purposes.
1. The origin of fiberglass filter paper
The fiberglass air filter paper industry originated in the 1940s. During World War II, the quality of aircraft navigation instruments produced in the United States was unstable, leading to high rework rates. Communication equipment also required frequent replacement of electronic components, and radar and submarine sonar systems often malfunctioned. Research revealed that the fundamental reason for this was the lack of cleanliness in the production environment, resulting in unstable quality and reliability of electronic components. Therefore, fiberglass air filter paper emerged, and in October 1940, fiberglass paper obtained a patent in the United States.

In the 1950s, the United States Atomic Energy Commission successfully developed efficient air filters that used fine fiberglass filter paper as the filtering medium. These high-efficiency air filters achieved a particle filtration efficiency of up to 99.99% for particles with 0.1-0.2 micrometers diameters. They applied these HEPA filters to the air supply systems of nuclear industry production workshops to collect radioactive dust.
2. The composition of fiberglass
Fiberglass can be divided into ordinary fiberglass (alkali-free and medium-alkali fiberglass), high-silica glass fibers, and special fiberglass based on composition.
Ordinary fiberglass
Its main components are silica dioxide, aluminum oxide, calcium oxide, boron oxide, magnesium oxide, sodium oxide, etc. Based on the composition of the glass raw materials, fiberglass can be classified into alkali-free fiberglass (R2O content less than 0.8%, belonging to aluminum borosilicate glass), medium-alkali fiberglass (R2O content 0.8% to 12%, belonging to sodium-calcium silicate glass with or without boron), high-alkali fiberglass (R2O content above 13%, belonging to sodium-calcium silicate glass), and special fiberglass.

Special glass fiber
Special glass fibers are new fibers developed to meet special usage requirements, with specific exceptional properties inherent in the fibers. They can be roughly categorized as follows: high-strength glass fibers, high-modulus glass fibers, heat-resistant glass fibers, alkali-resistant glass fibers, acid-resistant glass fibers, optical glass fibers, low dielectric constant glass fibers, conductive glass fibers, etc.
High-silica glass fibers
High-silica glass fibers have a silica dioxide (SiO2) content of over 96% and can withstand temperatures up to 900°C. In contrast, alkali-free glass fibers have only about 54% silica dioxide content, with a typical long-term working temperature of less than 300°C. However, the tensile strength of high-silica fibers (0.2N/Tex) is only half that of alkali-free fibers (0.4N/Tex).
High-silica glass fiber production primarily involves using a three-component sodium borosilicate (SiO2-B2O3-Na2O) glass. Various products, such as yarn and fabric, are made using the production process of ordinary glass fibers.
Acid leaching filters out the B2O3 and Na2O components, enriching the silica content to over 96% in a porous silica framework. Subsequently, the fibers are heat-treated at 600 to 800°C for final consolidation.
3. Glass fiber diameters
Glass fibers are cylindrical, so their diameter typically represents their thickness. Based on the diameter range, glass fibers produced by drawing can be classified into several categories (with diameter values in micrometers):
– Coarse fibers: typically with a single filament diameter of around 30 µm
– Primary fibers: with a single filament diameter greater than 20 µm
– Intermediate fibers: with a single filament diameter ranging from 10 to 20 µm
– Fine fibers (also known as textile fibers) with a single filament diameter ranging from 3 to 10 µm. Glass fibers with a single filament diameter of less than 4 µm are often called ultrafine fibers.
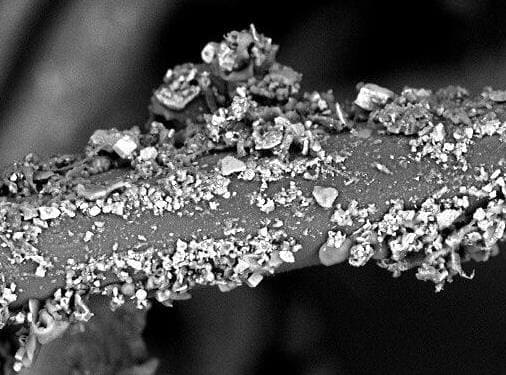
The diameter of the single filament affects the fibers’ properties and influences the production process, yield, and cost. Generally, fibers with diameters ranging from 5 to 10 µm are suitable for textile products. In comparison, fibers with 10 to 14 µm diameters are ideal for untwisted coarse yarns, non-woven fabrics, and short-cut fiber felts.
Currently, the mainstream diameter of glass fiber for filtering materials is around 6 micrometers.
4. The production process of glass fibers
Glass fibers can be classified into crucible and tank furnace processes according to the production technique.
Crucible Process
The crucible process involves a two-step forming process. It begins by melting glass raw materials at high temperatures to form glass globules, which are then remelted and rapidly drawn into glass fiber filaments. This process is characterized by high energy consumption, unstable forming processes, and low labor productivity, among other drawbacks.
Large-scale glass fiber manufacturers have primarily phased it out. Fibers produced using this process typically have uneven diameters and poor dispersion.
Tank furnace process
The pool kiln drawing method is a single-step forming process. Raw materials such as limestone are melted in a kiln to form a glass solution, which is then transported through channels to porous plates where it is rapidly drawn into glass fiber filaments. The kiln can be connected to multiple channels, with hundreds of porous plates simultaneously producing fibers. Simple procedures, energy efficiency, stable forming, high efficiency, and high productivity characterize this process.
It is conducive to large-scale automated production and has become the mainstream international production process. Glass fibers produced using this method account for over 90% of the global output.
The glass fibers are used for filtration purposes using this method.
5. High-temperature resistance and dimensional stability
Glass fiber can be used as a filter material for extended periods under operating conditions up to 260°C. Temperature control of the filtered gas is crucial in the design of dust removal equipment, and the high-temperature resistance of the filtering material plays a decisive role in the cost and operating expenses of dust removal equipment.

Excellent dimensional stability
At 260°C, glass fiber exhibits zero shrinkage, offering far superior dimensional stability compared to other synthetic fiber filter materials. When using glass fiber filter media, there is no need to worry about changes in air permeability or filtration area. For example, it doesn’t increase fabric tension or elongate filter bags due to shrinkage, avoiding issues like wrinkling and accelerated wear.
6. Tensile Strength at Break
High tensile strength and low elongation at break are other glass fiber filter materials characteristics. Therefore, when designing filter bags for dust removal, the requirement for the filter bag’s tensile strength can be ignored.
Comparison of Strength Between Glass Fiber Filter Material and Polyester Filter Material:
Filter Material | Machine Direction Strength | Cross Direction Strength |
Glass Fiber Filter Material N/50mm | 2400-4800 | 2000-4800 |
Synthetic Fiber Filter Material N/50mm | 600-3000 | 1000-2000 |
Last Summary
Generally, glass fiber is a high-performance inorganic non-metallic material of various types. Its advantages include good insulation, strong heat resistance, excellent corrosion resistance, and high mechanical strength.
In addition, glass fiber’s most prominent advantages lie in its high-temperature resistance, excellent dimensional stability, and high tensile strength. Glass fiber is resistant to chemical corrosion, except for hydrofluoric acid and high-temperature alkalis, making it stable in most other mediums.
One drawback of glass fiber is its relatively poor flexibility, but this can be significantly improved by controlling the fiber diameter and implementing surface chemical treatments.
Glass fiber can be classified according to glass composition, fiber diameter, and manufacturing process. Currently, the mainstream glass fiber used as filtering material has a single fiber diameter of 6 micrometers and is produced using the alkali-free pool kiln process.
In higher-grade filtration requirements, finer glass fibers are chosen as filter paper raw materials because this type of glass fiber filter paper has a higher fiber density, resulting in higher filtration efficiency.