A clean room is a special room with a highly clean environment, usually used in applications that require extremely high air quality and particle pollution control, such as electronics manufacturing, pharmaceuticals, biotechnology, and other industries.
As a leading HEPA filter manufacturer, I have been involved in many cleanroom projects. I wrote about several typical industrial clean room requirements and characteristics in this article; let’s look at them.
1. Characteristics of electronics manufacturing cleanrooms
It was first discovered that when there is dust in electronic components, these electronic components will malfunction. Clean rooms have become a necessary production environment for the electronics manufacturing industry.
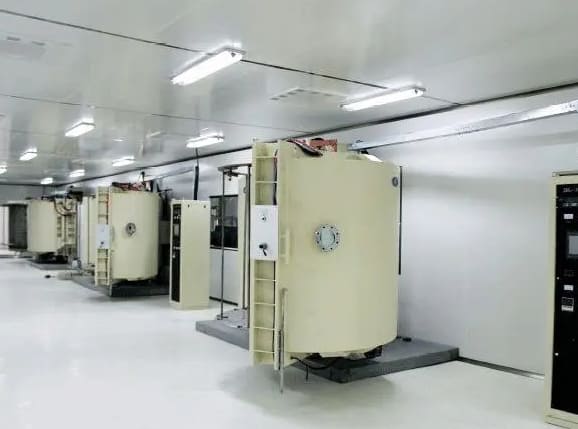
Characteristics of electronic manufacturer Cleanroom
The cleanliness level should be high, like level 10,000, and the air volume, temperature, humidity, pressure difference, and equipment exhaust should be controlled on demand.
Static electricity
This type of cleanroom has stringent requirements for static electricity.
Because static electricity is easily generated in a factory that is too dry, causing damage to CMOS integration.
In general, electronic factories should maintain a temperature of approximately 22°C, with relative humidity kept between 50-60%. Specialized clean workshops may have specific regulations regarding temperature and humidity. At this time, static electricity can be effectively eliminated.
Chip production, integrated circuit clean rooms, and disk manufacturing workshops are important components of clean rooms in the electronics manufacturing industry.
Noise level, static pressure, and amount of fresh air
Since electronic products have stringent requirements on indoor air environment and quality during manufacturing and production, the primary purpose is to control particles and floating dust. At the same time, strict regulations have been made on its cleanroom’s temperature, humidity, fresh air volume, noise, etc..
Noise level (empty state): Should not exceed 65dB(A).
The filling ratio of vertical flow clean rooms in electronics manufacturing factories should be at least 60%, and the horizontal unidirectional flow clean room should be at least 40%.
Ensure a static pressure difference of at least 10Pa between the clean room and outdoors and a minimum static pressure difference of 5Pa between cleanrooms of varying air cleanliness and non-clean areas.
The higher value between the following two should determine the clean room’s fresh air intake:
- The total exhaust air volume from the compensation room combined with the fresh air needed to sustain a positive indoor pressure value.
- Ensure the clean room receives a minimum supply of 40m3 of fresh air per person per hour.
In addition, the air supply volume of the clean room should take the maximum value of the following three items:
Air supply volume that ensures clean room air cleanliness level.
Determine the air supply volume of the clean room based on heat and moisture load calculations.
The quantity of fresh air provided to the clean room.
2. Characteristics of clean rooms in the pharmaceutical factory
Pharmaceutical factories not only have high equipment costs, complex production processes, and high requirements for cleanliness and sterility but also have strict requirements for the quality of production personnel.
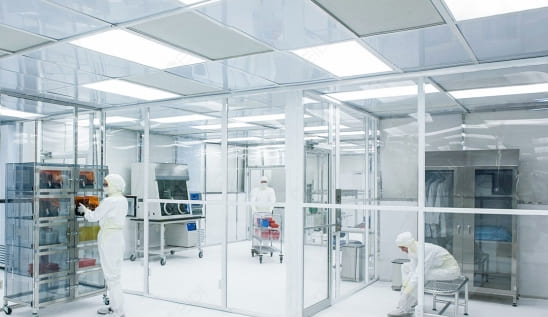
Clean area
The construction, equipment, and utilization of rooms (areas) aimed at controlling dust particles and microbial pollution in the environment are designed to prevent the introduction, generation, and retention of pollutants within the space.
Air lock room
An airlock room is an isolation area featuring two or more doors, typically between two or multiple rooms, such as those with varying cleanliness levels.
Setting up an airlock room is to control the airflow when people or materials enter or exit the cleanroom.
The airlock room is divided into a personnel and material airlock room.
Basic features of pharmaceutical clean rooms
Dust particles and microorganisms must be targeted for environmental control.
Level 100 or Partial level 100 in the context of level 10,000, level 1000, level 10000, and level 30000.
Clean room temperature: 18 to 26 degrees if no other special requirements, and relative humidity controlled at 45% to 65%.
Pollution control in pharmaceutical clean rooms: pollution source, dispersion process, and cross-contamination control.
The key technology of pharmaceutical clean rooms mainly lies in controlling dust and microorganisms. Microorganisms are the top priority in environmental control of pharmaceutical clean rooms.
3. Characteristics of clean rooms in the Spraying and packaging industry
Large-scale printing equipment has entered the cleanroom workshop, which can significantly improve the quality of printed products, and the product qualification rate has also increased considerably. This is also the best integration of the purification and printing industries.
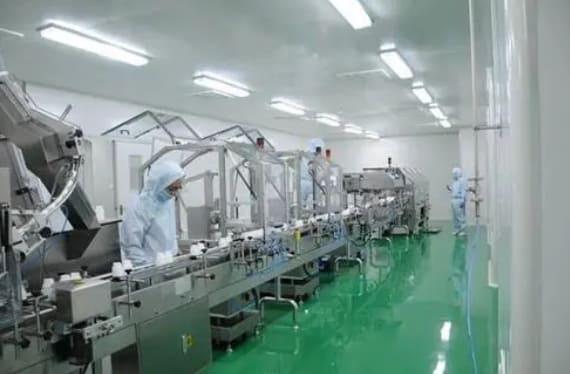
Dust-free Spraying
Dust-free Spraying is completed in an independent closed production workshop composed of steel sandwich panels, which can effectively filter the contamination of products by bad air and reduce the dust in the spraying area and the defective rate of products.
The application of dust-free technology further improves the appearance quality of products, such as TVs/computers, mobile phone casings, game consoles, PDA handheld computers, camera casings, stereos, hair dryers, cosmetic cases, etc.
Food packaging and pharmaceutical packaging
Today’s food and pharmaceutical packaging are all automated production lines and need a clean environment.
Features of food packaging cleanroom
The air supply volume is sufficient to dilute or eliminate indoor pollution.
The air in the cleanroom flows from the clean area to the areas with poor cleanliness, and the flow of contaminated air reaches a minimum level.
The airflow within the cleanroom is designed to ensure no areas of high-concentration accumulation in the room.
Features of Medicine package cleanroom
Environmental control requirements
Regularly monitor and document the quantity of airborne dust particles and viable microorganisms in the clean room of the packaging workshop. Ensure that the static pressure difference between packaging workshops of varying levels remains within the specified range.
The production area of highly allergenic products should be equipped with an independent air-conditioning system, and the exhaust must be purified.
Effective dust collection devices should be installed in rooms where dust is generated to prevent dust cross-contamination.
Cleanliness zones and air exchange numbers
The clean room cleanliness of pharmaceutical production and packaging workshops is divided into levels 100, 10,000, 100,000, and 300,000.
To determine the number of air changes in a clean room, it is necessary to compare various air volumes and select the maximum value. In practice, the air exchange rate is 300 to 400 times/h for level 100, 25-35 times/h for level 10,000, and 15-20 times/h for level 100,000.
Pharmaceutical packaging clean room temperature: Levels 100 and 10,000 are chosen at 20-23C (summer), levels 100,000 and 300,000 at 24-26C, and general areas at 26-27C.
Pressure difference
A clean room should have positive indoor pressure to maintain indoor cleanliness.
For clean rooms that produce dust, harmful substances, allergenic products, etc., external contamination must be prevented, or a relative negative pressure must be maintained between areas.
For the pressure difference in rooms with different cleanliness levels, the positive pressure must be maintained indoors, and the difference with adjacent rooms should be greater than 5Pa. The static pressure difference between the clean room and the outdoor atmosphere should be greater than 10Pa.
4. Characteristics of Clean Rooms in the Food Industry
Safety and hygiene in the food industry are essential in our daily lives. In addition to cleanliness, clean rooms in the food industry must ensure non-toxicity, ventilation, and anti-corrosion.
The floor of the clean room is made of non-slip, solid, impermeable, and corrosion-resistant materials and is flat and kept clean.
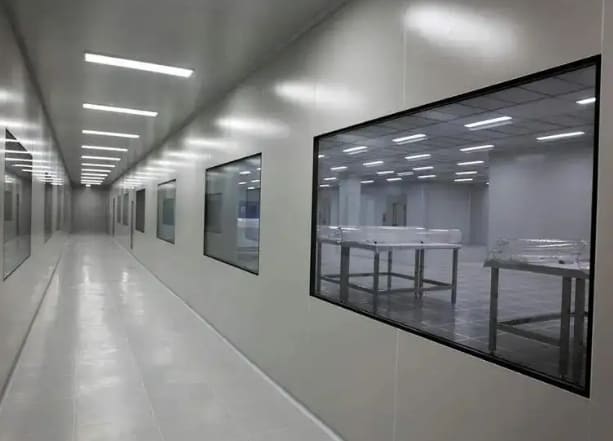
The workshop outlet and the drainage and ventilation areas connected to the outside world are equipped with anti-rat, anti-fly, and anti-insect facilities.
Clean room indoor walls, ceilings, doors, and windows are constructed of non-toxic, light-colored, waterproof, mildew-proof, non-shedding, and easy-to-clean materials.
5. Characteristics of Clean Rooms in the Optoelectronics
Optoelectronic optical clean rooms are generally suitable for electronic instrumentation, the automobile industry, the aerospace industry, photolithography, microcomputer manufacturing, and others. In addition to air cleanliness, they must also meet the requirements of static electricity elimination.
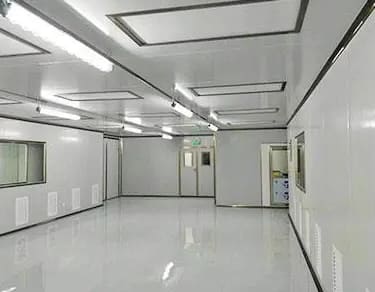
For example, the cleanliness level of LED clean rooms is usually Class 1,000, Class 10,000, or Class 100,000.
The characteristics of this type of cleanroom are
Temperature and humidity: The temperature is generally 24+2℃, and the relative humidity is 55+5%.
Fresh air volume: Since there are many operators in this type of cleanroom, the fresh air volume can take the following maximum value according to the following values:
10-30% of the total air supply volume in a non-unidirectional flow clean room.
The amount of fresh air required for compensate-room exhaust and maintain positive indoor pressure.
Ensure that the amount of fresh air per person per hour in the room is ≥40m3/h.
Air supply volume:
A larger air supply volume is required to meet such clean room’s cleanliness, heat, and moisture balance.
For a 300-square-meter workshop with a ceiling height of 2.5 meters, if it is a 10,000-level dust-free workshop, the air supply volume needs to be 300*2.5*30=22500m3/h (the number of air changes is ≥25 times /h).
If it is a 100,000-level purified and dust-free workshop, the air supply volume needs to be 300*2.5*20=15000m3/h (the number of air changes is ≥15 times/h).
6. Characteristics of Clean operating room
Clean operating room is a common form of clean room in the medical industry. It has the following characteristics:
Clean operating rooms take indoor microorganisms as the control target, operating parameters and classification indicators, and air cleanliness are necessary to guarantee conditions.
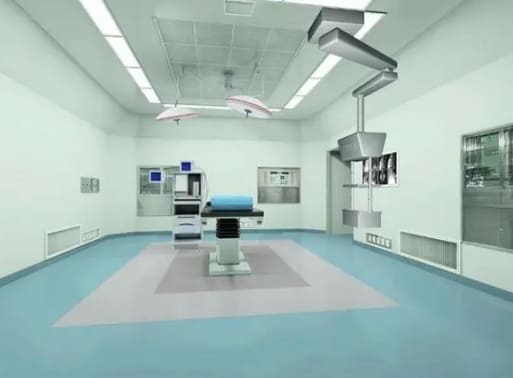
According to the requirements of different departments, the cleanliness level of the clean room can range from level 100 to level 100,000.
The layout of the clean operating room should be divided into two parts: clean area and non-clean area. The operating room and functional rooms directly serving the operating room should be located in a clean area.
When people and objects pass through areas with different cleanliness levels in the operating room, airlocks, buffer rooms, or transfer windows should be installed.
There are also clean rooms such as wards and biological laboratories in the medical field. Their characteristics are similar to high-level hospital clean rooms, so I won’t discuss them here.
Last summary
The last thing I want to mention is that no matter what kind of clean room it is, the air filter is the core component to achieve its cleanliness. The clean room HEPA filters we develop and produce specifically for the industry cleanroom will help you complete various clean projects and achieve different levels.