HEPA filter integrity testing tests the overall performance of a HEPA filter using specific particles and instrumentation under particular criteria. The result is usually a filtration efficiency value to verify that the filter is filtering at the required efficiency.
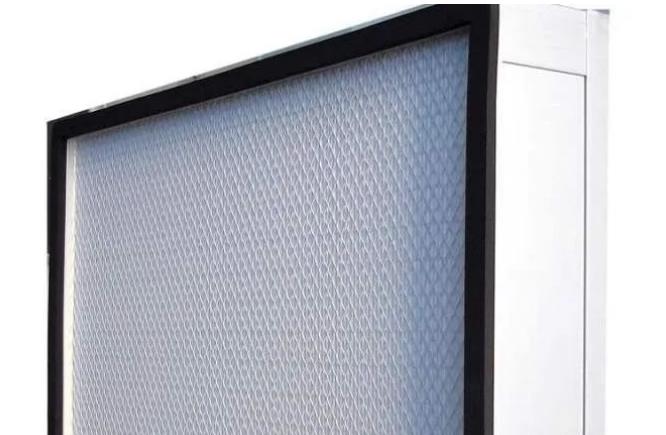
What Hepa stands for?
HEPA stands for High-Efficiency Particulate Air.
It is defined as a filter with an efficiency of 99.97% or more for particles with a particle size of 0.3μm.
As mentioned above, when we use a HEPA filter, it is necessary to express the efficiency together with the test method, e.g.
99.97% (0.3μm, DOP) means that the efficiency was tested using the DOP HEPA filter testing method.
When should HEPA filters be tested?
There are usually two situations where Hepa filters need to be tested.
1. After new HEPA filters have been manufactured and tested before it is shipped.
2. The new filter is installed in the cleanroom ceiling or HVAC system and must be tested before it can be officially operated.
Test the Hepa filter before they shipped from Manufacturer.
After decades of development in the Hepa filter industry, each country has developed its test methods and standards, and new HEPA filters are tested before they leave the factory.
The Common Hepa test methods are as follows:
Sodium flame method
1. This test method originated in the UK and was introduced in some European countries in the 1970s to 1990s.
The test dust source is the monodisperse phase sodium chloride salt spray.
The “amount” is the brightness of the hydrogen flame when containing salt mist. The test instrument is a photometer.
2. The brine is stirred by the compressed air, splashed, and dried to form a tiny salt mist and enter the air duct.
Samples are taken before and after the Hepa filter, and the salt mist-containing gas sample causes the hydrogen flame to turn blue and increase brightness.
The brightness of the flame is used to determine the salt mist concentration of the air and the efficiency of the Hepa filter for salt mist.
3. Some national standards specify an average salt spray particle diameter of 0.4 μm, but the measured results of existing devices are 0.5 μm. European measurements of the actual test salt spray particle median diameter are 0.65 μm.
4. With the popularity of the scanning method, the sodium flame method is no longer used in Europe. In some countries, the authorities are revising the original national standards, whether to abolish or to continue using the sodium flame method, both opinions of which are inconclusive.
5. Relevant standards for the sodium flame method: British BS3928-1969, European Eurovent 4/4.
The DOP aerosol test method
1. Originating in the USA, it is internationally available. The test dust source is 0.3μm monodisperse phase DOP (plasticizer commonly used in the plastics industry) droplets.
The “amount” is the degree of turbidity of the air containing the DOP. The instrument used to measure the dust is an aerosol photometer.
The air sample’s turbidity difference determines the filter’s efficiency in filtering DOP particles.
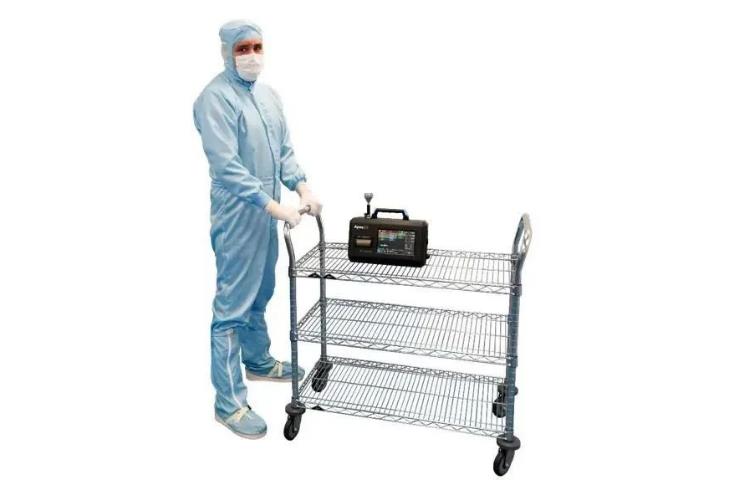
2. The DOP liquid is heated to a vapor, condensing under specific conditions into tiny droplets, leaving particles of around 0.3mm after removing the oversized and undersized droplets. The foggy DOP enters the ductwork system and introduces challenge aerosol to the Hepa filter.
The turbidity of the air sample before and after the filter is measured, and the upstream concentration of particles determines the filter’s efficiency in filtering 0.3μm dust.
3. The DOP method has been around for over 50 years, and this method used to be the most commonly used method for measuring HEPA filters internationally.
In the early days, it was thought that filters had the most difficulty filtering dust of 0.3μm, so it was prescribed to use 0.3μm dust to measure HEPA filters.
4. DOP contains a benzene ring and is suspected of being hazardous. Many laboratories have switched to alternatives with similar properties but without the benzene ring, such as DOS(Dioctylsebaeate). However, the test method is still called the “DOP method.”
5. DOP droplets of other particle sizes can be obtained by changing the dust generation parameters. This change led to the 0.1μm DOP method of measuring ultra-high efficiency filters in Europe and the USA 20-30 years ago. Sometimes, the measuring instrument can be changed to a condensation nodule laser particle counter.
6. The DOP method of measuring HEPA filters is also known as the “hot DOP method.”
The counterpart of the “cold DOP” method is the polydisperse phase DOP dust produced by the Laskin nozzle blower(compressed air bubbling in liquid and splashing to make atomized artificial dust), which is often used when scanning filters for testing.
7. Relevant standards for the DOP test method: US Military Standard MIL-STD-282.
Counting and scanning method
1. This test method is standard in Europe, similar to the USA, and closely followed by other countries—the current mainstream test method for HEPA filters internationally.
2. The primary measuring instrument is a high-flow laser particle counter or a condensation nucleus counter (CNC).
The entire air outlet surface of the filter is scanned and inspected with the counter, which gives the dust’s upstream concentration and particle size at each point.
This method not only measures the average efficiency of the filter but also allows a comparison of the local efficiency at each point.
3. European experience shows that the most easily penetrated dust particle size for HEPA filters is between 0.1 and 0.25μm. The most easily penetrated dust particle size for the test conditions is determined first. Then the filter is continuously scanned to measure the filter’s filtration effect on that particle size dust. Europeans call this method MPPS.
The USA standard states that only the 0.1 to 0.2μm interval will be measured.
4. The dust sources used in the tests are polydisperse phase droplets from Laskin nozzles or solid dust of defined particle size.
Sometimes, the filter manufacturer must use atmospheric or specific dust according to the customer’s requirements without aerosol challenge.
If a condensation counter is used in the test, a monodisperse phase test dust with a known particle size must be used.
5. Scanning a HEPA filter with a counter takes a long time.
To save time, filter manufacturers have combined four sets of high-flow sampling heads and laser measuring devices into one, which makes inspection much faster.
However, one scanning table still cannot keep up with the production speed of an ordinary hepa filter line, so filter manufacturers often need to deploy several scanning devices to handle the upstream challenge from production.
6. The count-and-scan method is the most rigorous method of testing HEPA filters, and the trend is to replace all other traditional methods with this method.
7. Counting and scanning method related standards: European EN 1882.1 to 1882.5 – 1998 to 2000, American IES-RP-CC007.1-1992.
Photometer scanning
1. The dust source is generally polydisperse phase droplets, such as DOP fumes from the Laskin nozzle.
The whole plane of the HEPA filter is scanned for leaks using a photometer.
2. This scanning method locates filter leaks quickly and accurately.
The dust source is polydisperse, and the photometer cannot determine the particle size of the dust. This scanning method gives little practical significance to the “filtration efficiency.”
3. Some manufacturers and users believe that the efficiency of a Hepa filter is already determined by strict control of the quality and specification of the filter paper and that a scan for leak detection alone will guarantee the filter’s quality.
4. No corresponding standard for the photometric scanning leak detection method exists. Still, this method is effective for quality control of the Hepa filter production process, and the test equipment used is relatively simple, so some manufacturers currently use this method.
The photometric scanning test bench can easily be converted into a counting scanning bench by spending money and buying a laser particle counter without any challenges.
Oil mist method
1. Formerly, West Germany and USSR used this method.
The source of dust is dispersed oil particulate. The “quantity” is the turbidity of the air containing the oil mist. The instrument is a turbidity meter. The air sample’s turbidity difference is used to determine the filtration efficiency of the HEPA filter for oil mist particles.
2. In Germany, paraffin oil is used with an oil mist particle size of 0.3 to 0.5 μm. Other standards specify an average diameter of oil mist of 0.28 to 0.34μm, with no specific provisions for the type of oil.
3. The oil mist method is now history in Germany. Germany was the first country to develop a national standard for counting and scanning in 1993.
The European standard EN 1882 was modeled on the German standard for the counting and scanning method.
4. Although some countries specify that the oil mist method can be used, filter manufacturers prefer another sodium flame method specified in the same standard.
Only some filter media manufacturers still use the oil mist when measuring filter material.
5. Oil mist method related standards: Germany DIN24184-1990.
Fluorometric method
Only used in France and is currently limited to testing of selected nuclear industry filters. The test dust source is sodium fluorescein dust produced by the sprayer.
In the test, samples are first taken before and after the Hepa filter, then the sodium fluorescein on the sampled filter paper is dissolved in water. The fluorescence brightness of the aqueous solution containing sodium fluorescein is measured under specific conditions. This brightness indirectly reflects the weight of the dust.
The difference in fluorescence brightness of the samples before and after the filter is used to determine the Hepa filter’s efficiency.
According to French standards, dust-generating devices produce dust with an average count size of 0.08μm and an average volume size of 0.15μm.
The fluorescence method could be less convenient, with measurements taken by sampling, cleaning the specimen, and then going to another location to measure the fluorescence.
French filter manufacturers often used the DOP rather than their prescribed fluorimetric method.
The French have made the European Association for Standardisation’s counting and scanning method a national standard.
When it comes to nuclear-grade HEPA filters, the fluorescence method is typically performed to meet the requirements of traditional customers.
The fluorescence method relevant standard is NF X44-011-1972, France.
Other testing methods for HEPA filters
Leak testing with variable airflow
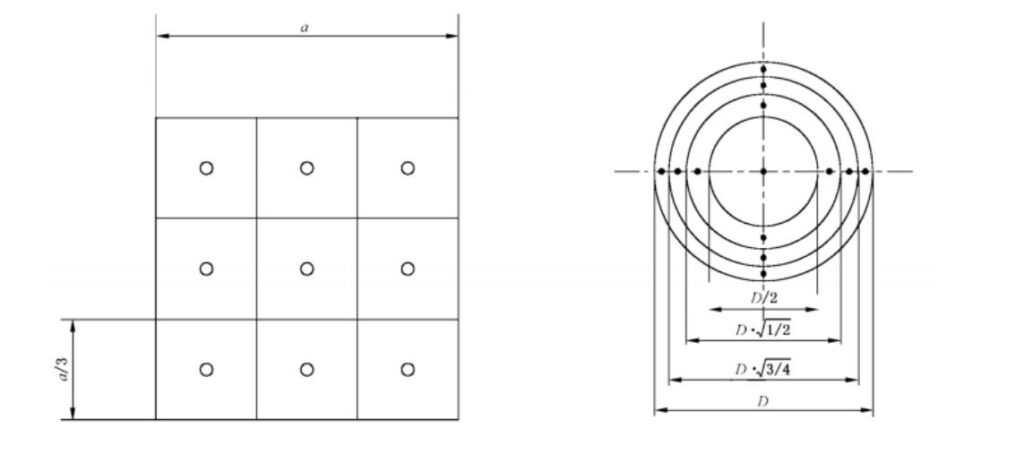
Using a standard test duct, if the HEPA filter’s efficiency decreases after reducing the flow rate, there must be a leak.
In past standards for HEPA filter test methods, variable air volume leak detection was often used.
The variable air volume check can only determine whether the filter leaks. It cannot locate the leak.
Smoke detection
In a dark room, smoke is emitted upstream of the Hepa filter, and a bright light is shone on the air outlet side so that when there is a leak in the filter, a wisp of smoke can be visibly seen at the leak.
This method allows the leak to be pinpointed for possible repair.
The smoke detection method is less elaborate but very effective.
Non-contamination test
Some customers are concerned about test aerosol contaminating the HEPA filter, and the filter manufacturer has to use the dust that the customer feels does not contaminate the filter during testing.
For example, semiconductor chip factories hate sodium salts, oil mist, and DOP aerosol challenge, and they often require manufacturers to use solid particulate dust that they consider safe.
Some pharmaceutical manufacturers require HEPA filters to be measured using dust directly from the outdoor atmosphere.
Hepa testing for replacement or installation
For the user, adequate HEPA filter testing refers to on-site leak testing after installing the HEPA filter in the cleanroom suite or facility.
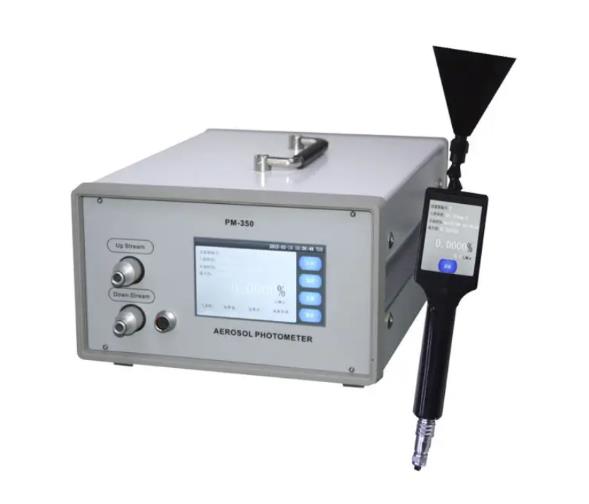
Purpose
The primary purpose is to probe for tiny holes and other defects in the Hepa filter, such as frame/gasket seals and leaks in the filter housing.
The purpose of leak detection is to probe the defects of the HEPA filter and its connection to the installation frame and the installation and to take the corresponding processes to ensure the cleanliness of the area.
What Aerosol is Used?
The leak test uses PAO(poly alpha olefin)/DOP aerosols.
Leak detection of HEPA filters is usually carried out by aerosol generation upstream of the filter using a PAO/DOP generator and a photometer to detect aerosol concentrations upstream and downstream of the filter to determine whether there is a leak.
The purpose of aerosol generation is because of the low concentration of dust particles upstream of the HEPA filter. Detecting leaks without aerosol generation using a particle counter alone is more difficult. Additional aerosol generation is required clearly and easily detect leaks.
Scanning for leaks
After aerosol generation upstream of the HEPA filter, the entire filter face, between the filter and the filter housing, between the HEPA filter housings and the installation frame, and between the installation frame and the static pressure box, is scanned for sealing.
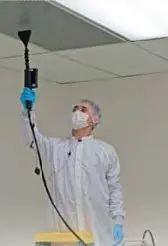
The sampling head is scanned approximately 1″ (approx. 2.54cm) from the filter face at a speed of no more than 5cm/s.
The scan is performed in a straight line back and forth with overlap between lines. During the test, an alarm (i.e., %LEAKAGE (leakage rate) exceeding 0.01%) indicates a leak.
Checking a HEPA filter takes about 5 min. During the test, the concentration of upstream aerosols should always be confirmed, and care should be taken to wear a protective face shield and eye protection during the test.
Leak detection criteria
Different standards also differ in the determination of leak detection results.
The US IEST-RP-CC034 stipulates that the on-site leak detection rate of 0.3um for Class C and D HEPA filters (photometric scanning leak detection method) is 0.01%.
The Europe EN1822 stipulates that as long as the local permeability of the tested filter does not exceed the specified local value, it will be qualified, and the corresponding local permeability of the H13 Hepa filter is 0.25%. However, it should be noted that the penetration here is based on a 0.3um monodisperse phase DOP aerosol test.