As countries increase their standards for industrial waste gas emissions, especially the high-temperature dusty flue gas emissions produced by heavily polluting industries, high-temperature filters have attracted more and more attention due to their excellent performance.
The core of the high-temperature filter lies in the filter material and high-temperature-resistant glue, which determine the filter’s temperature-resistant performance and filtration efficiency.
In the following article, I will discuss the key points of high-temperature filter media and fibers.
1. Nonwoven materials
Almost all air filter materials are nonwoven. Compared with woven fabrics, fibers directly reinforce nonwoven materials and have a three-dimensional network structure. They have the advantages of high porosity, good air permeability, and high filtration efficiency, so they are used as filter material.
According to the working temperature, fiber filter materials are divided into normal, high, and ultra-high temperature filter materials.
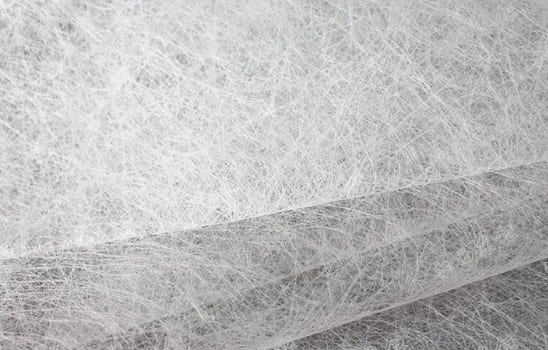
The main factor determining the temperature resistance of fiber filter materials is the thermal stability of the fiber. Currently, the fibers used for high-temperature filter materials that have been studied more include polyphenylene sulfide (PPS), polyimide (PI), polytetrafluoroethylene ( High-performance organic fibers such as PTEE), aramid and aramid sulfone (PSA), as well as inorganic fibers such as glass fiber, basalt fiber, and ceramic fiber.
Commonly used nonwoven fiber filter material processing methods include acupuncture, spun lace, electrospinning, and composite technologies.
2. Organic fibers
Organic fibers, which I usually call synthetic fibers, are used sparingly in high-temperature filters, but several fiber materials are still worth looking at.
PPS
PPS fiber is prepared by melting and spinning polyphenylene sulfide resin. It has the characteristics of good fiber spinnability, excellent mechanical properties, significant chemical corrosion resistance, and excellent thermal stability.
The limiting oxygen index of PPS fiber is 34 to 35, the melting point is as high as 280°C, and it can be used continuously at 190°C. Its needle-punched fiber filter material is widely used in high-temperature industrial flue gas dust filtration.
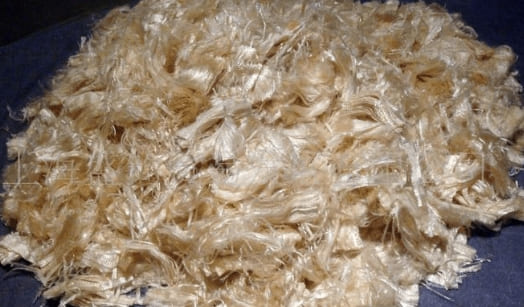
However, in high-temperature flue gas filtration containing strong oxidizing substances or high oxygen content (greater than 15%, wt), the application of PPS fiber is limited due to continuous oxidation.
Therefore, PPS fiber filter materials are generally coated or impregnated to improve their oxidation performance. On the other hand, they optimize its pore size structure and improve filtration efficiency.
PI fiber
The PI molecular chain contains an imide ring structure. The aromatic ring density in the molecular structure is relatively large. It has the characteristics of high/low-temperature resistance, radiation resistance, excellent mechanical properties, and good chemical stability.
It can be divided into four categories: iso-phenylene PI, soluble PI, polyamide-imide (PAI), and polyetherimide (PEI).
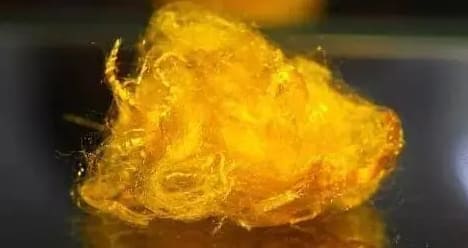
The decomposition temperature of PI fiber is as high as over 500°C. Its thermal stability and oxidation resistance are better than PPS fiber, but its acid and alkali resistance is poor, so it is suitable for low sulfur smoke filtration.
PTEE fiber
PTEE fiber is a high-performance fiber made from PTEE resin as raw material, which is processed by spinning, paste extrusion or filmmaking, and then cutting or fibrillation.
In its molecular structure, the binding solid force of carbon-fluorine bonds gives the fiber excellent chemical stability, corrosion resistance, and weather resistance. It can be used in the high-temperature range of 190 to 260°C.
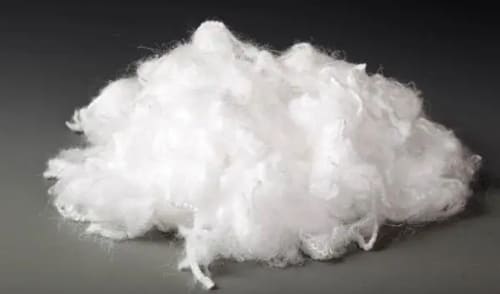
The prepared fiber filter material has a high strength retention rate at high temperatures and can resist corrosion by strong oxides and various acids and alkalis.
However, PTEE fiber has poor curling and antistatic properties, poor spinnability when used alone, and is more expensive. In addition, the filter bags made of it have poor creep resistance, so more attention should be paid to them during product design and use.
Aramid fiber
Aramid fiber is aromatic polyamide fiber, divided into meta-aramid and para-aramid, namely aramid 1313 and aramid 1414.
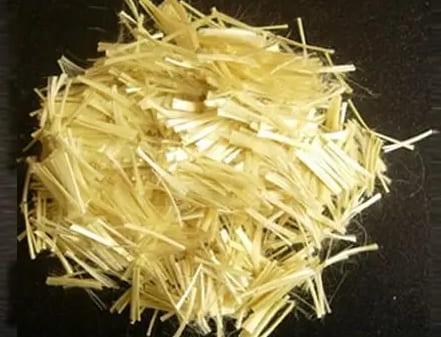
Among them, the high-temperature resistant filter material is mainly aramid 1313, which has high strength and modulus, as well as lightweight and alkali resistance. Its glass transition temperature is higher than 300°C, the thermal decomposition temperature is as high as 560°C, and it has excellent thermal stability. , but its hydrolysis resistance and acid resistance are slightly worse.
In addition, its production capacity is mainly concentrated in DuPont of the United States, AkzoNobel of the Netherlands, Teijin of Japan, Arcadis of Germany, etc., and the price is relatively high.
PSA fiber
PSA fiber is an artificial polyaramid organic fiber. Its molecular chain is composed of sulfone groups, amide groups, and benzene ring bonds. It has electrical insulation, radiation resistance, flame retardancy, dimensional stability at high temperatures, and mechanical and chemical properties. Good stability and other characteristics.
It still maintains 70% of its strength at 250°C. After being treated in hot air at 300°C and 250°C for 100 hours, its strength loss rate is only 20% and 10%, respectively.
But its internal structure will be destroyed when the temperature exceeds 350°C.
After the PSA fiber was treated with a strong acid solution with a mass fraction of 30% at 80°C, there was no significant decrease in strength. However, the strength loss was more obvious after being treated with a NaOH solution under the same conditions.
PSA fiber filter bags have excellent thermal and oxidative aging resistance, high-temperature dimensional stability, and good acid resistance, and they can be widely used in incinerator flue gas filtration.
3. Inorganic fiber
Compared with organic fibers, inorganic fibers are widely used in high-temperature filters. The most typical case is glass fiber.
Glass fiber
Glass fiber is an inorganic material used earlier in high-temperature flue gas dust removal. It has high-temperature resistance, corrosion resistance, good insulation, and low hygroscopicity. It can instantly withstand temperatures of 350°C and be used continuously in an environment of 280°C under alkali-free working conditions.
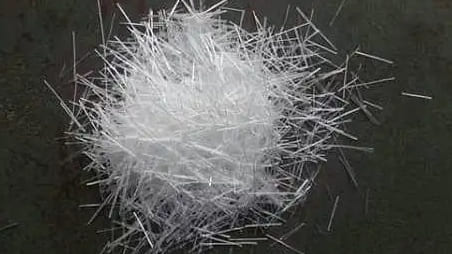
Glass fiber exhibits excellent chemical stability except for high temperature, strong alkali, and hydrofluoric acid. In addition, its surface is very smooth, which can improve the dust absorption performance of the filter material and has a low cost.
Glass fibers are usually ultra-finely processed to prepare filter materials, or composite filter materials are prepared by sandwiching between two mesh tires in the form of woven fabrics, weft-free cloths, etc., and then reinforcing them to prepare composite filter materials, which mainly play a reinforcing role.
At present, almost all high-temperature filters use glass fiber as filter material.
Ceramic fiber
Ceramic fiber is an inorganic, high-temperature resistant fiber material mainly composed of alumina, silicon carbide, or polysilicate.
It has high specific strength and specific modulus, corrosion resistance, oxidation resistance, lightweight, resistance to mechanical vibration, and high-temperature resistance, and its service temperature is as high as 800~1500℃.
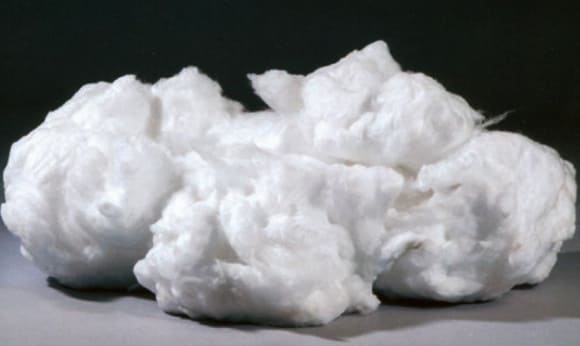
Other acids and alkalis have no noticeable corrosive effect, except for phosphoric acid, hydrofluoric acid, and strong acids. It is widely used in thermal insulation, fireproof barrier, and high-temperature filtration fields.
4. Needle-punched nonwoven
Needle-punched nonwoven materials are formed by the transfer and entanglement of fibers under the action of needles. They have a three-dimensional network structure. As filter materials, they have the characteristics of low cost, good air permeability, low resistance, and strong particle capture ability. They are currently the primary material of dust filter bags.
Due to needle marks, needle-punched fiber filter materials have large pores between fibers, and the filtration efficiency is not ideal, especially when the filtration efficiency of tiny particles is low.
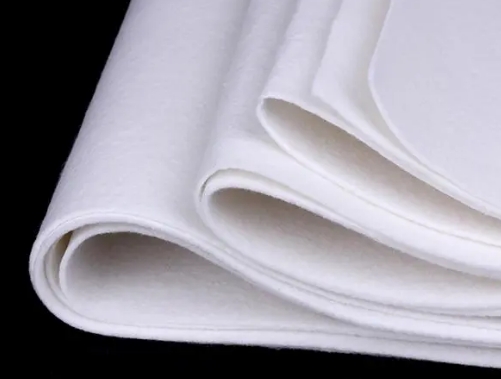
At present, post-finishing methods such as PTEE coating and PTEE emulsion dipping or coating are usually used to improve filtration performance.
After finishing, a layer of breathable microporous membrane can be formed on the surface of the filter material. On the one hand, it can improve the filter material’s filtration performance and accuracy and increase its service life. On the other hand, it can protect the filter material through the excellent chemical stability of PTEE.
5. Spunlaced nonwoven
Compared with acupuncture, on the one hand, hydroentanglement reinforcement technology causes less damage to fibers and can reduce the degree of damage to fibers or base fabrics.
On the other hand, water needles will form reflections on the surface of the trawl curtain after penetrating the fiber mesh. The fiber mesh will become denser under the dual action of direct water needles and reflection, which is beneficial for improving filtration performance.
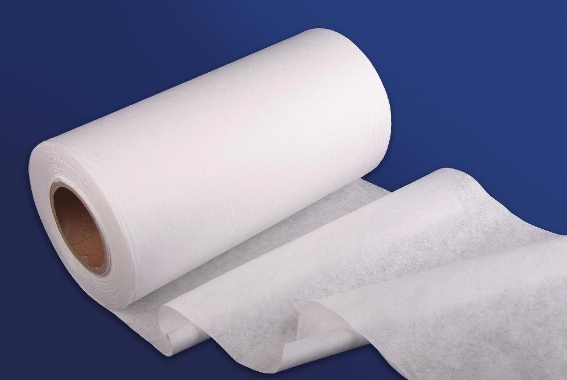
Compared with acupuncture, spun lace can make the fiber web denser, so the surface of the acupuncture fiber filter material can be processed through the spun lace process to improve its performance.
Composite filter materials can be prepared by consolidating the fiber layer to the base fabric through a spun lace process.
6. Wet process
At present, glass fiber filter paper is made using a wet process.
After thoroughly mixing glass fiber with different diameters (0.1-10 microns) and other components, a wet process is used to form a filter material with a thickness of about 0.4mm through mixing, surfing, drying, and other processes.

It has the characteristics of uniform fiber distribution, large dust-holding capacity, low resistance, and high strength. It is an ideal air filter material.
Last Summary
The fibers used in high-temperature filter materials are generally high-performance fibers, most of which are relatively expensive. In comparison, fiberglass materials have become the first choice for high-temperature filters due to their high filtration efficiency, large dust-holding capacity, and relatively low price. Of course, when filtering some special pollutants or in extremely high-temperature environments, we have to use other fiber materials.
It has become the direction of many manufacturers to develop new high-temperature-resistant fibers with lower costs and improve filter media performance through comprehensive utilization of processing methods and post-finishing.
As a leading high-temperature filter manufacturer, KOIN has served customers in more than 30 countries worldwide. Your filtration needs will get a fine solution here.